

yh86银河国际:炼焦技术交流:焦化基础知识汇总——化产回收篇
三、化产工艺 鼓冷岗位重点工艺技术指标参 数数 值初冷器前煤气总管温度82℃初冷器后煤气温度21℃循环水上水温度32℃低温水上水温度16℃初冷器阻力1.5KPa氮气加热器后氮气温度90℃电捕焦油器绝缘箱温度50~60℃电捕焦油器阻力0.5 KPa鼓风机出口煤气压力22 KPa鼓风机前吸力-500Pa鼓冷岗位产品(粗焦油)质量指标 粗焦油符合YB/T5075-93(2号指标)密度(2
三、化产工艺 鼓冷岗位重点工艺技术指标 参 数 数 值 初冷器前煤气总管温度 82℃ 初冷器后煤气温度 21℃ 循环水上水温度 32℃ 低温水上水温度 16℃ 初冷器阻力 1.5KPa 氮气加热器后氮气温度 90℃ 电捕焦油器绝缘箱温度 50~60℃ 电捕焦油器阻力 0.5 KPa 鼓风机出口煤气压力 22 KPa 鼓风机前吸力 -500Pa 鼓冷岗位产品(粗焦油)质量指标 粗焦油 符合YB/T5075-93(2号指标) 密度(20) 1.13~1.22g/ml 含水 ≤4.0% 灰分 ≤0.13% 粘度(E80) ≤4.2% 甲苯不溶物(无水基) ≤9% 脱硫工段 脱硫岗位技术指标 预冷塔后煤气温度 30℃ 预冷塔阻力 500Pa 出脱硫塔煤气温度 33℃ 脱硫塔脱硫液温度 35℃ 出脱硫塔煤气压力 20KPa 进再生塔压缩空气压力 0.55MPa 塔后煤气含硫 <300mg/m3 硫磺含硫 80% 硫铵工段 硫铵岗位技术指标 入饱和器煤气温度 70℃ 出饱和器煤气温度 55℃ 饱和器阻力 ≤2000Pa 干燥后硫铵含水 0.5% 母液酸度 3.5~4.0% 硫铵产品质量指标 氮含量(以干基计) ≥21% 含水 ≤0.5 游离酸含量 ≤0.08% 粗苯工段 粗苯岗位技术指标 出终冷塔煤气温度 25℃ 终冷塔阻力 <1000Pa 洗苯塔阻力 <1500Pa 洗苯塔后煤气含苯量 4g/m3 管式炉富油出口温度 180~185℃ 脱苯塔顶部温度 90~93℃ 脱苯塔底贫油温度 170~175℃ 粗苯岗位产品质量指标 粗苯 符合YB/T5022-93(溶剂用) 密度(20℃) ≤0.900g/ml 馏程:180℃前馏出量(重) ≥91% 水分 室温(18~25℃)下目测无可见的不溶解水 一.工艺简介: 来自焦炉~80℃左右的荒煤气首先通过气液分离器实现气液分离,分离出的粗煤气由上部出来,进入横管初冷器分两端冷却。 分离下来的焦油、氨水和焦油渣一起进入机械化氨水澄清槽分离。 初冷器分上、下两段,煤气上进下出,冷却水下进上出,煤气在初冷器上段与冷却管内的循环水换热,从~80℃冷却~45℃,循环水由32℃升至40℃,然后煤气进入初冷器下段与冷却管内的制冷水换热,煤气从~45℃冷却到21~22℃,制冷水由16℃升至23℃。 初冷后煤气从下部进入电捕焦油器,自下而上通过电捕焦油器蜂窝管,依靠电捕内高压场对气体的电离作用,气体中的焦油雾滴被电离下来(电捕后要求煤气中含焦油﹤20mg/m3),电捕后煤气进入离心鼓风机进行加压之后送往硫铵工段。 初冷器的煤气冷凝液分别由初冷器上段和下段流出,分别经初冷器水封槽后进入上、下段冷凝液循环槽,分别由上段冷凝液泵和下段冷凝液泵加压后送至初冷器上、下喷淋,如此循环使用,以清除管壁上的焦油、萘等杂质,保证了初冷器的冷却效果,多余冷凝液由下段冷凝液循环泵抽送至气液分离器前荒煤气管道。 经常化验冷凝液焦油含萘量,定期从机械化氨水澄清槽压至上、下段冷凝液槽一部分轻质焦油,以提高冷凝液焦油的吸萘效果。从而保证初冷却效果。 从气液分离器分离的焦油、氨水与焦油渣自流至机械化氨水澄清槽,澄清后分离成三层,上层为氨水,中层为焦油,下层为焦油渣。分离的氨水溢流至循环氨水槽,然后由循环氨水泵抽送至焦炉集气管循环喷洒冷却荒煤气。 定期用高压氨水泵抽送一部分送焦炉清扫集气管。当初冷器电捕焦油器、洗脱苯终冷器塔需要清扫时,从循环氨水泵后抽出一部分定期清扫,多余的氨水由循环氨水泵抽送至剩余氨水槽,剩余氨水中的焦油充分沉降分离后用剩余氨水泵送至硫铵工段进行蒸氨。 焦油调至焦油中间槽贮存,当达到一定液位时用焦油泵送至焦油槽贮存脱水,定期用焦油泵送至罐区或装车平台装车外售。 分离的焦油渣定期送往锅炉煤场作燃料。 各设备的蒸汽冷凝液均接掺入凝结水槽,定期用凝结水泵送至锅炉房经电捕焦油器捕集下来的焦油排入电捕水封槽,由电捕水封槽液下泵送至气液分离器前荒煤气总管,当沉淀管用循环氨水冲洗时,冲洗液排入电捕水封槽,用电捕水封槽液下泵加压送至气液分离器前荒煤气管道,鼓风机机体及煤气管道的冷凝液均流入鼓风机水封槽,鼓风机及其煤气管道的冷凝液均流入鼓风机水封槽,然后由鼓风机水封槽液下泵,加压送至气液分离器前荒煤气总管。 各设备的排净现场用软管引至废液收集槽,定期用废液收集槽液下泵送至机械化氨水澄清槽澄清分离。 为保护环境将各贮槽的尾气集中后,由排气风机抽送至排气洗净塔,用循环水循环洗涤后排放,为保证洗涤效果,循环水由水道循环 系统连续补入,由排气洗净泵连续抽送一部分送往生化处理。 二.工艺流程图(见上页): 三.技术指标: 1. 初冷器部分: 1).初冷器前煤气温度:78~82℃ 2).初冷器后煤气温度: 21~22℃ 3).循环水入设备温度:~32℃ 4).循环水回水温度:~40℃ 5).制冷水进水温度:~16℃ 6).制冷水回水温度:~22℃ 7).初冷前吸力:﹤1500MPa 8).初冷后吸力:~2500MPa 9).初冷器阻力:≯1500MPa 10).各初冷器出口温差:﹤3℃ 2.电捕焦油器部分: 1).煤气含氧量:﹤0.8%(1.0%报警,1.2%联锁) 2).处理煤气量:48000~58000m3/h 3).绝缘箱温度:90~110℃ 4).二次电压:40~60KV 5).二次电流:﹤500MA 6).电捕阻力:~500Pa 7).电捕后煤气中焦油含量:﹤20mg/m3 8).绝缘箱充氮气量:75m3/h 9).氮气压力:﹥15KPa 3.鼓风机部分: 1).风机前吸力:3500~5000Pa 2).风机后压力:~18000Pa 3).机前煤气进口温度:~25℃ 4).机后煤气出口温度:﹤45℃ 5).机组轴瓦温度正常值:﹤60℃(75℃报警,85℃联锁) 6).鼓风机轴位移:≯0.4㎜(0.5㎜报警,0.8联锁) 7).临界转速:3000~3300r/min 8).振动:≯7道 9).电动机轴承温度:﹤60℃(75℃报警,85℃联锁) 10).电动机定子温度:~120℃(135℃报警,≥145℃联锁) 11).电动机额定电流:I=68.3A 4.油站系统: 1).油冷却器后油温:~35℃ 2).至各润滑点油压:0.11~0.18MPa(﹤0.08MPa辅助油泵启动、﹥0.25MPa停止) 3).液力偶合器进口油温:~45℃ 注:油站电加热系统:当温度低于20℃时电加热自启,高于35℃ 时电加热自停。 4).润滑油指标:46#汽轮机油 5.槽区、泵房: 1).循环氨水泵出口压力:0.4~0.5MPa 2).高压氨水泵出口压力:~3.0MPa 3).剩余氨水泵出口压力:~0.4MPa 4).各电机温度:﹤65℃ 5).循环氨水温度:70~75℃ 6).机械化氨水澄清槽油水界面:1.5~1.8m 7).循环氨水槽液位:3.5~4.0m 8).各泵的轴承温度:﹤70℃ 6.焦油质量标准: 密度(20℃):1.15~1.2g/cm3 含萘:≮7.0% 水份:<4.0% 灰分:<0.13% 甲苯不溶物:3.5%~7% 粘度(E80):<4 四.岗位职责: ㈠.鼓风机岗位职责: 1. 在班长和工段长的领导下,负责本工区的生产操作,设备维护和保养,环境保护及清洁文明生产。 2. 稳定风机操作,保证焦炉集气管压力、风机吸力、压力等各项工艺指标符合要求。 3. 负责备用风机盘车,风机系统冷凝液吹扫工作,保证排液管畅通。 4. 负责初冷器的开停车及清扫工作,保证初冷器后煤气温度符合 规定。 5. 负责电捕焦油器的开停车及清扫工作。 6. 负责检查煤气系统冷凝液排液管,水封及初冷器上、下段喷洒系统的调节及维护,喷洒液配比的调整工作。 7. 严格执行操作规程,不违章指挥、不简化操作。 8. 认真检查、发现、处理、汇报生产中的异常情况,做到早汇报,早处理。 9. 认真写生产记录,字迹要求清晰,记录要准确。 ㈡.冷凝工岗位职责: 1. 负责冷凝泵房内循环氨水泵、高压氨水泵、焦油泵、凝结水泵、洗涤泵的开、停、倒换操作。 2. 负责机械化氨水澄清槽的调油工作,保证机械化氨水澄清槽焦油渣焦油、氨水分离良好,确保焦炉氨水不带焦油。 3. 负责焦油槽区蒸汽加热系统,焦油脱水工作,负责焦油外箱装车工作。 4. 负责尾气洗净塔的操作工作。 5. 负责废液收集槽,循环氨水槽,剩余氨水槽,凝结水槽的生产工作,及时外送剩余氨水、凝结水。 五.岗位操作规程: ㈠.正常操作: 1. 初冷器的正常操作: 1).调节初冷器上、下段冷却水量,保证上段、下段煤气温度合适, 使初冷后煤气温度符合技术规定。 2).检查初冷器阻力,确保上、下段冷凝液喷洒管畅通,定期用热氨水冲洗初冷器,防止阻力增大。 3).调节各初冷器的进、出口煤气量,调节冷却水量,确保各初冷 器出口煤气温差不大于3℃. 4).检查初冷器及初冷器前后煤气管线排液管及水封排液管是否 畅通,每班需吹扫一次,确保各退液管及水封畅通。 5).检查设备、管道、阀门、有无破裂、跑、冒、滴、漏现象,出现及时处理。 2.鼓风机的正常操作: 1).检查风机轴承温度、轴位移、机体振动是否正常,严禁机组在 临界转速位运行,确保机组运行平稳,电机电流稳定。 2).保证鼓风机吸力、压力在规定值内,从而确保集气管压力符合 要求。根据焦炉煤气量变化,调节液力偶合器转速,或大循环管来控制焦炉集气管压力。风机吸力、压力稳定。 3).风机冷凝液管每班至少用蒸汽清扫一次,冬季两次以确保畅 通。 4).检查油站润滑系统、油温、油压是否正常,确保油站油位、油 温、油压符合要求。 5).检查液力偶合器油箱油位符合要求,检查偶合器进、出口油温, 出口油压是否正常。 6).定期化验润滑油的质量是否符合要求,如不合格需及时更换, 定期给各系统润滑点按规定加润滑油脂。 7).检查风机水封槽冷凝液液位,及时启动液下泵外排。 8).检查风机各润滑点回油情况,发现异常及时查找原因处理。 9).备用风机每班盘车一次,每次盘1/4圈。 10).做好原始记录,每小时记录一次,要求填写真实、清晰、公 正。 3.电捕焦油器的正常工作: 1).调整控制好电捕绝缘箱温度在90~110℃. 2).调整好绝缘箱瓷瓶保护氮气压力、流量,使绝缘箱不被污染。 3).检查电捕阻力情况,定期用热氨水冲洗。 4).根据煤气含焦油量调整二次电压,使电捕焦油器后煤气含焦油量合格。 5).检查电捕排液管及水封是否畅通,及时外排冷凝液,每班清扫 一次排液管。 6).稳定煤气含氧量,煤气含氧量超标时及时查明原因消除。 4.冷凝岗位各泵槽正常操作: 1).调整循环氨水泵泵压,使焦炉集气管氨水喷洒压力保持在 0.2~0.25MPa,高压氨水泵定期启动,压力能满足集气管清扫要求。 2).保证各槽的液位正常,不溢槽,不抽空。 3).按时巡查设备运行情况,检查各泵的润滑情况,要求视镜2/3. 4).调整剩余氨水泵流量,使其与氨水处理岗位处理量适合。 5).按时排放沉积在各氨水槽底部的焦油,保证外供氨水不带焦 油。 6).检查机械化氨水澄清槽刮板机的运行情况,减速机的油质油 量,出渣情况及时运走油渣。 7).调节机槽油水界面,及时调油,保证焦油不带水,氨水不带油。 8).检查废液收集槽,凝结水槽液位及时外送。 9).检查尾气洗净塔运行情况,洗净液喷洒效果,定期外排废水, 补充新鲜循环水,确保洗涤效果。 10).焦油槽脱水,蒸汽加热保温使焦油符合要求,焦油的输送管 道,在输送前后都必须用蒸汽吹扫干净。 ㈡.开、停车及倒换操作: ⑴.初冷器的开、停、倒换操作: 1.开初冷器: 1).检查各阀门的严密情况,确保其灵活好用。 2).检查上、下段的冷却水系统供水是否正常。 3).各水封槽已注满水,各处仪表齐全完好。 4).打开欲开初冷器的上、下段排液管阀门,用蒸汽吹扫确保畅 通。 5).打开初冷器顶部放散,打开通入器体的蒸汽(或氮气)阀门, 通入蒸汽(或氮气),待放散冒出大部分蒸汽(或氮气)后,取样做含氧分析合格后,关小蒸汽(或氮气)。 6).煤气系统运行正常后,按离心泵的启动操作步骤启动上、下 段冷凝液喷洒泵,调节泵压、循环量,使系统形成循环。 7).打开上段循环冷却水,入口阀门,慢慢打开初冷器出口阀。 8).打开煤气入口阀通煤气,同时关闭蒸汽(或氮气)阀,关闭 放散。 9).煤气走通后,根据煤气温度情况开下段冷却水上水阀出口阀, 调节冷却水量,使初冷器后煤气温度符合要求。 2.停初冷器: 1).关闭煤气进出口阀门。 2).依次关闭循环水,制冷水入口阀门,并将各段冷却水放空。 3).关闭冷凝液循环喷洒泵出口阀,停上、下段喷洒泵,并将管 道内冷凝液放空,并用蒸汽吹扫冷凝液管。 4).打开顶部放散,打开蒸汽管道阀,赶初冷器内煤气,待放散 冒出大量蒸汽后,关闭蒸汽,关闭放散,待冷却后放净器内冷凝液,初冷器通入氮气处于备用状态。 3.倒初冷器: 1).按开工操作开待用初冷器。 2).正常后,关闭停用初冷器煤气进出口阀门,关闭冷却水进出 口阀门,并放掉系统积液,清扫做为备用或进行检修。 3).调整运行初冷器冷却水量,使温度符合要求。 4).启动运行初冷器的冷凝液喷洒系统。 4.热氨水冲洗运行初冷器: 1).初冷器阻力>1000Pa时,初冷后煤气温度不符合要求,需清 扫。 2).打开循环氨水泵至初冷器的氨水管阀门,停上段冷凝液喷洒 泵。 3).打开入初冷器的上段氨水阀,对初冷器进行热氨水喷洒清洗。 4).注意煤气温度变化,及时调节冷却水量。 5).清扫完毕后,关闭氨水阀,启动上段冷凝液喷洒泵。 ⑵.电捕焦油器的开停、倒换操作: 1. 开电捕焦油器: 1).电捕水封槽已注满水,确认下液管畅通,各阀门处于关闭状 态。 2).电器仪表经检查处于正常状态,绝缘箱通蒸汽加热达到90~ 110℃.使其达到技术指标。 3).做电捕空投试验正常,电工确认绝缘和电气部分的绝缘电阻合 格。 4).打开放散管,向电捕内通蒸汽(或氮气),待放散冒出大量蒸 汽(或氮气),做含氧量分析合格后,关小蒸汽(或氮气)阀门,使其保持微正压。 5).打开氮气进绝缘箱管道上阀门,调节氮气压力,流量符合规定。 6).关闭放散管和蒸汽阀门,送煤气,打开煤气出、入口阀门(入 口快,出口慢)。 7).向电捕送电,逐级升压至规定值,注意电捕二次电压,电流变 化。 8).打开下液管阀门,检查退液管排液是否畅通,做好记录。 2.停电捕焦油器操作: 1).按电捕操作要求逐渐由高档降至抵挡,电捕操作电压降至0, 切断电源,把三点开关转为接地、放电。 2).打开电捕旁通阀,关闭煤气出、入口阀,使煤气走旁通。 3).关闭电捕绝缘箱,馈电箱氮气保护阀。 4).用蒸汽清扫排液管,保证排液管畅通。 5).用热氨水冲洗电捕沉降,或打开电捕顶部放管,用蒸汽吹扫电 捕,赶净器内煤气。 6).清扫完毕,当电捕内温度降至<60℃时,关闭蒸汽放散管,通 入少量氮气保压备用。 7).放净器内积液,关闭退液管,关闭绝缘箱加热系统。 3.倒换电捕焦油器操作: 1).按开工操作要求开启用电捕。 2).启用电捕运行正常后,停需停电捕,切断电源,确认接地放电。 3).关闭停电捕进出口阀门,清扫器体,放净器内冷凝液,关闭绝 缘箱加热系统,使其处于备用状态。 4.电捕焦油器的清扫: ⑴.蒸汽清扫: 1).按电捕焦油器的停工步骤停电,接地放电,停绝缘箱、蒸汽 加热、氮气保护系统,开煤气旁通阀,关闭电捕进出口煤气阀。 2).打开顶部放散,通蒸汽清扫30min. 3).打开氮气管阀,关闭蒸汽,待电捕冷却至常温后,关闭氮气, 关闭放散,按开工步骤启动电捕。 ⑵.氨水清扫: 1).电捕焦油断电接地放电。 2).煤气走旁通,关闭煤气出入口阀。 3).打开电捕热氨水清扫管道阀向电捕通热氨水,清扫。 4).清洗完毕后,打开电捕出、入口阀,关闭旁通阀,按电捕开工 程序通电开工。 ⑶.鼓风机的开、停、倒换操作: 1. 鼓风机的开机操作: 1).准备好听音棒、测震仪、温度计、压力表及记录本。 2).检查电器线路、仪表、绝缘等机械状况良好。 3).检查油站油位、油温、油路阀门开闭情况是否合乎技术规定, 液力偶合器油位是否正常。 4).电工、仪表工、检修工、操作工等相关人员全部到位,准备就 绪。 5).启动润滑油泵,备用油泵调为自动,调整油压、油温,观察回 油情况是否正常。 6).清扫机体及风机前后排液管,确保畅通,水封槽液位正常。 7).盘车,并上好风机端盖。 8).打开机体下排液管的蒸汽阀门,向机体通蒸汽暖机,机体温度 达到60℃~70℃时,关蒸汽,排净机体冷凝液。 9).关闭机体排液管及机前机后排液管阀门。 10).打开风机煤气入口阀~2/3,活动出口阀,大循环管阀开~ 1/2,偶合器调节先打至手动。 11).通知变电所送高压电,通知焦炉地下室等相关单位,准备开 机。 12)接上级主管下达指令,启动电机。. 13).手动调节偶合器执行机构,启动输出轴低速运行,观察各处 油温、油压、回油,各设备的轴承温度,设备本体温度等是否正常。 14).调整风机的进出口阀门开度。 15).根据煤气量的变化,慢慢提升风机转速,当接近临界转速时, 快调偶合器使风机快速越过临界区。 16).首次开工时,由于煤气量较少,为了保证集气管压力稳定和 鼓风机正常运行,应以大循环管来进行调节,此后随煤气量的增大逐渐关小大循环,直至完全关闭。根据焦炉集气管压力的变化由液力偶合器调节。 17).当油站油温到38~40℃时开大冷却器冷却水,偶合器油温至 55~58℃时,开大冷却器冷却水,使油温符合要求。 18).当风机运行稳定后,打开风机机体及负压等各处排液管阀门 排液,确保排液畅通。 19).当风机运行稳定后,与焦炉上升管,地下室联系,把鼓风机 液力偶合器执行器由手动切换为自动(焦炉π型翻板,地下室翻板自动)。 20).鼓风机运行正常后转入正常生产,及时巡检,查看各项指标是否符合要求,做好相关记录。 2.鼓风机的停机操作: 1).与各级主管,变电所,焦炉等有关单位联系,共同做好停机、 停煤气准备。 2).接上级主管停机指令后,将偶合器调节由自动转为手动,手动 缓慢降低偶合器输出转速(当快降到临界转速时,快调执行器,使风机转速能够快速降到临界转速以下),同时慢关煤气出口阀。 3).待风机转速降至0时,关闭煤气进出口阀门,切断电机,停主 电机。 4).通蒸汽清扫风机机体和各冷凝液排液管,同时进行盘车,把转 子上的附焦油清扫干净,清扫完毕后停汽,凉机,放掉冷凝液。 5).各处轴承温度降至40℃时,油站油温降至30℃时,关闭油冷 却器冷却水,停油站油泵。 6).停车后半小时盘车一次,待机体及轴承温度降至常温后每班盘 车一次。 7).长时间停机,应将冷却器内液体放空,防止冬季冻坏设备。 3.鼓风机的倒机操作: 1).倒机操作前应先与相关单位联系好,通知相关岗位做好倒机准 备。 2).做好准开机的准备工作,偶合器调节切换为手动,开准开风机 进口约2/3,活动出口,在主管领导的指挥下,按开机的操作步骤启动准开风机电机。 3).启动准开风机主电机手动调节缓慢提升准开风机的转速,慢慢 开出口阀门,同时逐渐降低停风机的转速,慢慢关小停风机的出口阀门,使其平衡,保证焦炉、集气管压力稳定。 4).至待停机的转速降至0时,关闭煤气出、入口阀,同时准开风 机的进出口阀开度正常,转速调至正常转速。 5).停风机按停机后操作做为备用。 ⑷、排气洗净塔操作: 1. 开工操作: 1).向尾气液封槽注满水。 2).从洗净塔上部向塔内注入来自管道的循环水,使塔底水位达到 液位显示2/3处,关闭循环水注水阀。 3).打开排气洗净泵循环管路上的阀门,开通循环管线。 4).按离心泵的启动步骤启动排气洗净泵形成循环,并调节循环喷 洒量,符合排气洗净要求。 5).打开排气风机入口阀,启动排气风机,把各储槽放散排气送入 洗净塔。 6).待排气洗涤循环正常后,适当打开送生化处理装置阀门,适量 排出洗涤废水送生化处理,并打开新鲜循环水注水阀,保持塔 底液位稳定。 2.停工操作: 1).关闭排气风机的入口阀门,停排气风机。 2).关闭循环水注水阀。 3).停洗涤泵后,将泵体及管道内液体放净。 4).放净塔内洗涤液。 ⑸.机械化澄清槽的开工操作: 1.开工操作: 1).与电工联系,检查电器设备的状况。 2).清理器内杂物,钳工确认刮板机运行和液位调节器装置正常。 3).打开澄清槽的氨水出口,混合液入口阀,待液体充满后,给电 启动刮板机。 4).待机械化氨水澄清槽内焦油液位达到~1.7m时,打开焦油出 口管道,调节液位调节器,保持机槽焦油、氨水界面稳定。 2.停工操作: 1).关闭冷凝液入口阀和氨水出口阀。 2).将槽内焦油压空,停止刮板机。 3).将槽内液体放净。 ⑹.离心泵的开、停、倒换操作: 1.离心泵的开启流程: 提前检查泵箱油位正常,仪表、电器、贮槽液位正常,阀门灵活好用,管道畅通,准备工作做好。 注:焦油泵需用蒸汽清扫泵前后管道,冬季还需预热油泵至盘车灵活。 2.离心泵的停车流程: 注:焦油泵停泵后需用蒸汽吹扫泵体,泵前后管道,防止堵塞。 3.离心泵的倒泵流程: ㈢、特殊操作: 1.鼓风机部分: ⑴ .突然停电: 停高压电: 1).迅速关闭煤气出口阀门,主电机开关打至停机位置。 2).液力偶合器调节由自动转换为手动,调节执行机构归零。 3).关闭煤气入口阀门,吹扫机体及各下液管。 4).与相关部门联系,询问停电原因,做好记录,做好来电后开 车准备。 停低压电: 若油站油泵未停,不影响风机运行,坚持生产,通知有关领导,联系有关部门尽快供电。若风机因低压控制电路停电造成停机时,按停机处理。 ⑵.突然停水: 油冷却器启用另一路水,坚持生产,通知有关领导。 通知有关部门,尽快恢复供水,若两路水都停,机组轴瓦温 度超过规定值后,且水还没有供给,立即停车。做好供水恢复后,开车准备。 ⑶.突然停蒸汽: 询问相关部分原因,尽快恢复,以便于吹扫排液管。 ⑷.遇到下列情况之一鼓风机司机有权紧急停机: 1).机组突然发生强烈振动或机体内有磨刮声时; 2).任一轴承或密封处发生冒烟时; 3).进油管路上油压下降至0.08MPa,而连锁辅助油泵投入工作后,油压仍低于0.05MPa时; 4).轴承温度急剧升高到75℃以上,采用各种措施仍不能下降时; 5).鼓风机转子的轴向位移大于0.5㎜,采用各种措施后轴向位移继续增大时; 6).风机前煤气管道着火时; 7).油箱的油位下降至最低油位线,加入新油,油位仍继续下降且得不到控制时; 2.电捕焦油器部分: ⑴.突然停电: 立即拉下电捕电闸,接地放电,并向上级主管汇报,做好来 电后开工准备,做好记录,询问停电原因送电时间,若停电时间较长则按停工处理。 ⑵.突然停汽: 注意电捕绝缘箱温度,当绝缘箱温度低于80℃时,停电捕 供电,询问停汽原因,恢复供冷时间,做好记录,做好送汽后开车准备。 3.初冷器部分: ⑴ .突然停循环水: 短时停水,增大初冷器制冷水量,控制器后煤气温度﹤30℃, 长时间停水,将备用初冷器投入,增加冷却水量维护生产,询问停水原因及恢复供水时间,做好记录。 ⑵ .突然停制冷水: 短时停水,增大初冷器循环水量,控制器后煤气温度﹤ 30℃,长时间停水,使用备用初冷器,增大循环水量维护生产,询问停水原因及恢复供水时间,做好恢复供水正常生产操作准备。 ⑶ .突然停循环水,制冷水两路水: 两路水都停后,直接停产,询问停水原因供水时间,做好 供水后开工准备。 4.冷凝岗位部分: ⑴.突然停电: 切断所有运行泵的电机电源,并关闭出口阀门,与相关部门联系,若短时恢复供电,做好准备;若停电时间长,按停泵操作,注意各槽液位变化,控制好各槽不满流。 焦油泵在正常送油时发生停电,立即切断电源,关闭出口阀门;若停电时间长,需用蒸汽吹扫送油管道。 ⑵.突然停冷却水 与综合供水泵房联系,询问停水原因及时间,若时间短,坚持生产,加强检查;若时间长,请示有关部门,按停工操作处理。 ⑶.突然停仪表风: 将自控调节阀门前后阀门关闭,打开旁通阀,用旁通阀人工 手动调节维护生产,来风后,关闭旁通阀,打开调节阀前后阀门,恢复调节自控做好记录。 注:冷鼓工段全部停电,送电后,首先必须先将循环氨水泵启动,循环正常后,再将风机开启,之后依次启动其它设备。 六.岗位安全规则: 1.对高压电机的开停,严格执行操作制度。 2.禁止吸烟,严禁将火种带入本岗位。 3.劳保用品必须穿戴齐全方可进入操作岗位进行操作,不许穿铁钉、铁掌鞋,进入化产区。 4.检查有气液体溢出槽罐设备时,要求站在上风侧,手扶牢栏杆。 5.在风机房和煤气设施上检修时,严禁使用铁制工具拷打,应用铜 制工具。 6.电捕焦油器运行状态下,禁止上电捕焦油器,停电检修时,必须先断电,接地放电,防止电捕内残余静电击伤。 7.需进入设备、罐、槽、塔内检查,检修时,必须清扫后做气体分析试验合格后方可进入。人孔全部打开,保持通风,进入煤气设备时,必须将煤气进出口堵上盲板。 8.检查电机、风机轴承,各泵轴承温度情况时,以手背面触摸,禁 用掌心。 9.开关高处阀门,至少2人配合操作,固定好扶梯,防止跌滑。 10.装焦油及取样时,要站在一侧,防止热油溅出烫伤。 11.出现煤气泄露时,应首先通风散气,预防发生中毒和爆炸事故。 12.本工段区域内动火检修必须事先办理动火许可证,并确切落实安 全措施。 13.电捕初次投用前,本体应进行气密性试验合格后,方可投入使用。 14.第一次启动电气设备不成功,必须通知专业维护人员进行检修处 理后,方可再次送电,50KW以上电机严禁连续启动三次。 15.电捕焦油器绝缘箱通氮气保护,发现氮气异常时,应立即断电。 16.电捕焦油器煤气含氧分析仪报警,联锁自动跳闸后,需查明原因, 进行有效处理后,方可重新投入使用。 17.操作室,操作台等设备不准有明线,发现漏电现象及时通知电工 处理,清除隐患。 18.发现有跑、冒、滴、漏现象,及时通知相关人员处理。 19.保证电机运行平稳,各项指标符合要求,发现异常,及时处理。 20.各运行设备联轴器无防护罩,禁止运行。 七.设备维护生产保养规程: ㈠.设备概要: 1.非标设备: ⑴ .初冷器A、B、C: 3台 长×宽×高:4484×3300×~32866 F总=5144㎡ 上段:F=3026㎡ 壳程:焦炉煤气~-0.001MPa(表) 管程:循环水0.4MPa(表)30~40℃ 换热管:57×3×4500 n=3800 下段:F=2118㎡ 壳程:焦炉煤气~-0.002MPa(表) 管程:制冷水0.4MPa(表)16~23℃ 换热管:57×3×4500 n=2660 ⑵.气液分离器:1台 2400×7315 V总=24m3 介质:焦炉煤气、氨水、焦油 温度:~80℃ 压力:~-0.001MPa(表) ⑶ .机械化氨水澄清槽:2台 型号:71.067 长×宽×高:24616×4590×~5686 V全=340m3 介质:焦油、氨水、焦油渣 温度:~80℃ 压力:常压 附传动装置:电动机直联型三级卧式行星摆线针轮减速机 型号:XWSD2.2-1174-1/16555 电动机:电压:380V 功率:N=2.2KW 转速:1430r/min 总减速比:i=16555×2.5238=41781.5 刮板运输机:工作能力:~400kg/h焦油渣 工作速度:3.7555m/h ⑷.循环氨水槽:2台 8000×5100 V总=256m3 立式 温度:~80℃ 压力:常压 ⑸.剩余氨水槽:2台 8250×8600 V全=460m3 立式 介质:氨水、水蒸汽及冷凝液 温度:~80℃ 压力:常压 附加热装置:加热蛇管:57×3.5 F=40.8㎡ 管内温度:~158℃ 管内压力:~0.5MPa ⑹.焦油中间槽:1台 5200×4500 V总=95.6m3 立式 介质:焦油、水蒸汽及冷凝液 温度:~80℃ 压力:常压 附加热装置:加热蛇管:57×3.5 F=~12㎡ 管内温度:~158℃ 管内压力:~0.5MPa ⑺.焦油槽:2台 8800×8200 V总=500m3 立式 介质:焦油、水蒸汽及冷凝液 温度:~75℃ 压力:常压 附加热装置:加热蛇管:57×3.5 F=48㎡ 管内温度:~158℃ 管内压力:~0.5MPa ⑻.初冷器水封槽:6台 800×3000 V总=1.5m3 立式平顶 介质:煤气冷凝液 温度:20~45℃ 压力:常压 ⑼.鼓风机水封槽:1台 长×宽×高=2600×1000×4000 V全=10.4m3 立式平顶 介质:煤气冷凝液 温度:~35℃ 压力:常压 ⑽.鼓风机水封槽:1台 长×宽×高=2600×1000×4000 V 介质:煤气冷凝液 温度:~35℃ 压力:常压 ⑾.电捕水封槽:1台 长×宽×高=2600×1000×4000 V 介质:电捕液 温度:~35℃ 压力:常压 ⑿.凝结水槽:1台 3000×2500 V总=18m3 介质:蒸汽冷凝液 温度:~90℃ 压力:常压 ⒀.废液收集槽:1台 4000×4000 V总=50m3 介质:焦油、氨水 温度:~75℃ 压力:常压 3 全=10.4m3 全=10.4m立式锥顶 立式平顶 立式平顶 立式平顶 ⒁.上段冷凝液循环槽:1台 2200 L=6000 V全=21.3m3 卧式 介质:煤气冷凝液 温度:~45℃ 压力:常压 ⒂.下段冷凝液循环槽:1台 2200 L=6000 V全=21.3m3 卧式 介质:煤气冷凝液 温度:~45℃ 压力:常压 ⒃.尾气液封槽:1台 400×600 V总=0.075m3 立式平顶 介质:焦油、氨水 温度:常温 压力:常压 ⒄.排气洗净塔:1台 1500×~17720 V总=23.6m3 立式平顶 介质:槽区尾气、循环水 温度:~40℃ 压力:常压 丙装聚丙烯花环填料 25×9乱堆 2. 标准设备 ⑴.离心鼓风机:2台 型号:D1450-1.11/0.81 Q=1450m3/h △P=30000Pa 输送介质:焦炉煤气 介质重度:~0.45㎏/m3 进口压力:~-3500~-5000Pa 进口温度:22~25℃ 转速:4340r/min 轴功率:936KW 附:电机 功率:1000KW 电压:10KV 2台 附:防爆调速型液力偶合器(配套板式冷却器) 2台 附:润滑油系统(含防爆油站,高位油箱等) 2台 附:变速器 2台 ⑵.排风机:2台 型号:9-19NO.4A2右90 Q=970m3/h △P=3665Pa 输送介质:含氨尾气 附电机 功率:2.2KW 电压:380V 型号:YB90L-2W ⑶.循环氨水泵:2台 型号:350S-75B Q=828~1225m3/h H=59~47.5m 单级,双吸中开式离心泵 输送介质:氨水 介质重度:~1000㎏/m3 温度:~75℃ 转速:1470r/min 附电机 功率:250KW 电压:10KV 型号:Y450-4C 2台 ⑷.剩余氨水泵:2台 型号:IS65-40-250 Q=15~30m3/h H=82~78m 单级,单吸式离心泵 输送介质:氨水 温度:~75℃ 转速:2900r/min 附电机 功率:15KW 电压:380KV 型号:Y132S2-2 2台 ⑸.焦油泵:2台 型号:80AY-60 Q=50m3/h H=60m 单级,单吸式离心泵 输送介质:焦油 温度:~80℃ 转速:2950r/min 附电机 功率:18.5KW 电压:380KV 型号:Y160L-2 2台 ⑹.上段冷凝液循环泵:2台 型号:IS100-65-200 Q=60~120m3/h H=54~47m 单级,单吸式离心泵 介质:煤气冷凝液 温度:~45℃ 转速:2900r/min 附电机 功率:22KW 电压:380KV 型号:YB180M-2W 2台 ⑺.下段冷凝液循环泵:2台 型号:IS150-125-315 Q=120~240m3/h H=34~29m 单级,单吸式离心泵 介质:煤气冷凝液 温度:~30℃ 转速:1450r/min 附电机 功率:30KW 电压:380KV 型号:YB200L-4W 2台 ⑻.凝结水泵:2台 型号:ISR50-32-200 Q=7.5~15m3/h H=48~52.5m 单级,单吸式离心泵 介质:氨水 温度:~75℃ 转速:2900r/min 附电机 功率:5.5KW 电压:380KV 型号:Y132S1-2 2台 ⑼.鼓风机水封槽液下泵:2台 型号:LYA40-160 Q=28m3/h H=28m 单级,单吸式耐腐蚀液下泵 介质:煤气冷凝液、焦油、氨水 温度:~30℃ 转速:2960r/min 第30 / 34页 插入深度:L=3800㎜ 附电机 功率:7.5KW 电压:380KV 型号:YB132S2-2W 2台 ⑽.废液收集槽液下泵:2台 型号:LYA40-160 Q=28m3/h H=28m 单级,单吸式耐腐蚀液下泵 介质:煤气冷凝液 温度:~50℃ 转速:2960r/min 插入深度:L=3800㎜ 附电机 功率:7.5KW 电压:380KV 型号:YB132S2-2 2台 ⑾.电捕水封槽液下泵:1台 型号:LYA40-160 Q=28m3/h H=28m 单级,单吸式耐腐蚀液下泵 介质:煤气冷凝液 温度:~30℃ 转速:2960r/min 插入深度:L=3800㎜ 附电机 功率:7.5KW 电压:380KV 型号:YB132S2-2W 1台 ⑿.排气洗净泵:2台 型号:IS50-32-200 Q=7.5~15m3/h H=52.5~48m 单级,单吸式离心泵 输送介质:氨水 温度:~75℃ 转速:2900r/min 附电机 功率:5.5KW 电压:380KV 型号:Y132S1-2 2台 ⒀.高压氨水泵:2台 型号:D46-50×7 Q=30~55m3/h H=388.5~322m 多级,单吸式离心泵 输送介质:氨水 第31 / 34页 温度:~75℃ 转速:2950r/min 附电机 功率:75KW 电压:380KV 型号:Y280S-2 2台 ⒁.手动单梁起重机:1台 型号:SDQ-10 起重量:10吨 LK=13米 起升高度:6米 轨宽:70㎜ 附:手拉葫芦 起重量:10吨 起升高度:10米 型号:HS10 1台 ⒂.手动单轨小车:1台 型号:SDX-5 起重量:5吨 起升高度:5米 附:手拉葫芦:起重量:5吨 起升高度:5米 型号:HS5 1⒃.带斗小推车:3台 ⒄.滤油机:1台 型号:LY150 配电机:功率:3KW 电压:380V ⒅.电捕焦油器:2台 型号:FD248-II-A(D) 工作介质:含焦油、萘雾滴的焦炉煤气 处理煤气量:48000~58000m3/h 煤气温度:22~25℃ 煤气压力:~-3~-5KPa 绝缘箱夹套蒸汽压力:0.4~0.5 MPa 蒸汽加热管压力:0.4~0.5 MPa 顶部清洗液压力:﹥0.3 MPa 沉淀极: 结构型式:蜂窝式 单管规格:正六边形内切圆:250×4500 台 第32 / 34页 有效截面积:13.4㎡ 附:高压恒流电源(户内型)1.0A/60KV 2台 ㈡.设备维护保养: 1. 操作人员必须做到“四懂四会”:懂结构、懂原理、懂性能、懂用途、会使用、会维护保养、会排除故障,会小修。 2. 操作人员要精心操作正确使用设备,严格执行操作规程。 3. 严格控制工艺技术条件,做到不超温、不超压、不超负荷。 4. 经常巡检各运行设备的润滑油系统,保证油位合乎要求。 5. 各阀门要定期加油,保证灵活好用。 6. 备用运转设备每班盘车一次,备用风机每班盘车1/4. 7. 各运行设备在启动前首先盘车,并查看附属设备及各处润滑情况,存在缺陷的设备严禁投入运行。 8. 风机油箱润滑油定期取样化验,油质有变化时及时处理,每月滤油一次,定期清洗滤芯。 9. 定期化验液力偶合器油箱油质,不合格时必须及时更换。 10.备用电动鼓风机每月做空投试验一次,由电工检查绝缘情况二次,并要求电工在交接本上做好记录。 11.风机运行周期为3个月,到期要由检修人员进行全面检查、测试,确定能否继续运行,并将备用风机进行检查保养。 12.电捕焦油器氨水喷头每年清扫一次,更换堵塞喷嘴。 13.让电器人员经常检查电捕电器系统绝缘性能。 14.正常情况下,氨水泵3各月倒换一次,进行全面检查。 第33 / 34页 15.50KW以上的电机严禁连续启动三次。 16.所有设备和环境做到卫生清洁,无跑、冒、滴、漏现象,做到文明生产。 17.设备定期刷漆,防腐,提前做好设备夏季降温,冬季防冻工作。 18.设备冷却水及冷却器冷却水水温,水压及时检查调节,防止水温过高损坏设备和油中串水。 19.严格执行巡回检查制度,实行“听、摸、查、看、闻”五字方针,发现异常及时处理。 一.工艺简介: 来自焦炉~80℃左右的荒煤气首先通过气液分离器实现气液分离,分离出的粗煤气由上部出来,进入横管初冷器分两端冷却。 分离下来的焦油、氨水和焦油渣一起进入机械化氨水澄清槽分离。 初冷器分上、下两段,煤气上进下出,冷却水下进上出,煤气在初冷器上段与冷却管内的循环水换热,从~80℃冷却~45℃,循环水由32℃升至40℃,然后煤气进入初冷器下段与冷却管内的制冷水换热,煤气从~45℃冷却到21~22℃,制冷水由16℃升至23℃。 初冷后煤气从下部进入电捕焦油器,自下而上通过电捕焦油器蜂窝管,依靠电捕内高压场对气体的电离作用,气体中的焦油雾滴被电离下来(电捕后要求煤气中含焦油﹤20mg/m3),电捕后煤气进入离心鼓风机进行加压之后送往硫铵工段。 初冷器的煤气冷凝液分别由初冷器上段和下段流出,分别经初冷器水封槽后进入上、下段冷凝液循环槽,分别由上段冷凝液泵和下段冷凝液泵加压后送至初冷器上、下喷淋,如此循环使用,以清除管壁上的焦油、萘等杂质,保证了初冷器的冷却效果,多余冷凝液由下段冷凝液循环泵抽送至气液分离器前荒煤气管道。 经常化验冷凝液焦油含萘量,定期从机械化氨水澄清槽压至上、下段冷凝液槽一部分轻质焦油,以提高冷凝液焦油的吸萘效果。从而保证初冷却效果。 从气液分离器分离的焦油、氨水与焦油渣自流至机械化氨水澄清槽,澄清后分离成三层,上层为氨水,中层为焦油,下层为焦油渣。分离的氨水溢流至循环氨水槽,然后由循环氨水泵抽送至焦炉集气管循环喷洒冷却荒煤气。 定期用高压氨水泵抽送一部分送焦炉清扫集气管。当初冷器电捕焦油器、洗脱苯终冷器塔需要清扫时,从循环氨水泵后抽出一部分定期清扫,多余的氨水由循环氨水泵抽送至剩余氨水槽,剩余氨水中的焦油充分沉降分离后用剩余氨水泵送至硫铵工段进行蒸氨。 焦油调至焦油中间槽贮存,当达到一定液位时用焦油泵送至焦油槽贮存脱水,定期用焦油泵送至罐区或装车平台装车外售。 分离的焦油渣定期送往锅炉煤场作燃料。 各设备的蒸汽冷凝液均接掺入凝结水槽,定期用凝结水泵送至锅炉房经电捕焦油器捕集下来的焦油排入电捕水封槽,由电捕水封槽液下泵送至气液分离器前荒煤气总管,当沉淀管用循环氨水冲洗时,冲洗液排入电捕水封槽,用电捕水封槽液下泵加压送至气液分离器前荒煤气管道,鼓风机机体及煤气管道的冷凝液均流入鼓风机水封槽,鼓风机及其煤气管道的冷凝液均流入鼓风机水封槽,然后由鼓风机水封槽液下泵,加压送至气液分离器前荒煤气总管。 各设备的排净现场用软管引至废液收集槽,定期用废液收集槽液下泵送至机械化氨水澄清槽澄清分离。 为保护环境将各贮槽的尾气集中后,由排气风机抽送至排气洗净塔,用循环水循环洗涤后排放,为保证洗涤效果,循环水由水道循环 系统连续补入,由排气洗净泵连续抽送一部分送往生化处理。 二.工艺流程图(见上页): 三.技术指标: 1. 初冷器部分: 1).初冷器前煤气温度:78~82℃ 2).初冷器后煤气温度: 21~22℃ 3).循环水入设备温度:~32℃ 4).循环水回水温度:~40℃ 5).制冷水进水温度:~16℃ 6).制冷水回水温度:~22℃ 7).初冷前吸力:﹤1500MPa 8).初冷后吸力:~2500MPa 9).初冷器阻力:≯1500MPa 10).各初冷器出口温差:﹤3℃ 2.电捕焦油器部分: 1).煤气含氧量:﹤0.8%(1.0%报警,1.2%联锁) 2).处理煤气量:48000~58000m3/h 3).绝缘箱温度:90~110℃ 4).二次电压:40~60KV 5).二次电流:﹤500MA 6).电捕阻力:~500Pa 7).电捕后煤气中焦油含量:﹤20mg/m3 8).绝缘箱充氮气量:75m3/h 9).氮气压力:﹥15KPa 3.鼓风机部分: 1).风机前吸力:3500~5000Pa 2).风机后压力:~18000Pa 3).机前煤气进口温度:~25℃ 4).机后煤气出口温度:﹤45℃ 5).机组轴瓦温度正常值:﹤60℃(75℃报警,85℃联锁) 6).鼓风机轴位移:≯0.4㎜(0.5㎜报警,0.8联锁) 7).临界转速:3000~3300r/min 8).振动:≯7道 9).电动机轴承温度:﹤60℃(75℃报警,85℃联锁) 10).电动机定子温度:~120℃(135℃报警,≥145℃联锁) 11).电动机额定电流:I=68.3A 4.油站系统: 1).油冷却器后油温:~35℃ 2).至各润滑点油压:0.11~0.18MPa(﹤0.08MPa辅助油泵启动、﹥0.25MPa停止) 3).液力偶合器进口油温:~45℃ 注:油站电加热系统:当温度低于20℃时电加热自启,高于35℃ 时电加热自停。 4).润滑油指标:46#汽轮机油 5.槽区、泵房: 1).循环氨水泵出口压力:0.4~0.5MPa 2).高压氨水泵出口压力:~3.0MPa 3).剩余氨水泵出口压力:~0.4MPa 4).各电机温度:﹤65℃ 5).循环氨水温度:70~75℃ 6).机械化氨水澄清槽油水界面:1.5~1.8m 7).循环氨水槽液位:3.5~4.0m 8).各泵的轴承温度:﹤70℃ 6.焦油质量标准: 密度(20℃):1.15~1.2g/cm3 含萘:≮7.0% 水份:<4.0% 灰分:<0.13% 甲苯不溶物:3.5%~7% 粘度(E80):<4 四.岗位职责: ㈠.鼓风机岗位职责: 1. 在班长和工段长的领导下,负责本工区的生产操作,设备维护和保养,环境保护及清洁文明生产。 2. 稳定风机操作,保证焦炉集气管压力、风机吸力、压力等各项工艺指标符合要求。 3. 负责备用风机盘车,风机系统冷凝液吹扫工作,保证排液管畅通。 4. 负责初冷器的开停车及清扫工作,保证初冷器后煤气温度符合规定。 5. 负责电捕焦油器的开停车及清扫工作。 6. 负责检查煤气系统冷凝液排液管,水封及初冷器上、下段喷洒系统的调节及维护,喷洒液配比的调整工作。 7. 严格执行操作规程,不违章指挥、不简化操作。 8. 认真检查、发现、处理、汇报生产中的异常情况,做到早汇报,早处理。 9. 认真写生产记录,字迹要求清晰,记录要准确。 ㈡.冷凝工岗位职责: 1. 负责冷凝泵房内循环氨水泵、高压氨水泵、焦油泵、凝结水泵、洗涤泵的开、停、倒换操作。 2. 负责机械化氨水澄清槽的调油工作,保证机械化氨水澄清槽焦油渣焦油、氨水分离良好,确保焦炉氨水不带焦油。 3. 负责焦油槽区蒸汽加热系统,焦油脱水工作,负责焦油外箱装车工作。 4. 负责尾气洗净塔的操作工作。 5. 负责废液收集槽,循环氨水槽,剩余氨水槽,凝结水槽的生产工作,及时外送剩余氨水、凝结水。 五.岗位操作规程: ㈠.正常操作: 1. 初冷器的正常操作: 1).调节初冷器上、下段冷却水量,保证上段、下段煤气温度合适, 使初冷后煤气温度符合技术规定。 2).检查初冷器阻力,确保上、下段冷凝液喷洒管畅通,定期用热氨水冲洗初冷器,防止阻力增大。 3).调节各初冷器的进、出口煤气量,调节冷却水量,确保各初冷 器出口煤气温差不大于3℃. 4).检查初冷器及初冷器前后煤气管线排液管及水封排液管是否畅通,每班需吹扫一次,确保各退液管及水封畅通。 5).检查设备、管道、阀门、有无破裂、跑、冒、滴、漏现象,出现及时处理。 2.鼓风机的正常操作: 1).检查风机轴承温度、轴位移、机体振动是否正常,严禁机组在临界转速位运行,确保机组运行平稳,电机电流稳定。 2).保证鼓风机吸力、压力在规定值内,从而确保集气管压力符合要求。根据焦炉煤气量变化,调节液力偶合器转速,或大循环管来控制焦炉集气管压力。风机吸力、压力稳定。 3).风机冷凝液管每班至少用蒸汽清扫一次,冬季两次以确保畅通。 4).检查油站润滑系统、油温、油压是否正常,确保油站油位、油温、油压符合要求。 5).检查液力偶合器油箱油位符合要求,检查偶合器进、出口油温,出口油压是否正常。 6).定期化验润滑油的质量是否符合要求,如不合格需及时更换,定期给各系统润滑点按规定加润滑油脂。 7).检查风机水封槽冷凝液液位,及时启动液下泵外排。 8).检查风机各润滑点回油情况,发现异常及时查找原因处理。 9).备用风机每班盘车一次,每次盘1/4圈。 10).做好原始记录,每小时记录一次,要求填写真实、清晰、公正。 3.电捕焦油器的正常工作: 1).调整控制好电捕绝缘箱温度在90~110℃. 2).调整好绝缘箱瓷瓶保护氮气压力、流量,使绝缘箱不被污染。 3).检查电捕阻力情况,定期用热氨水冲洗。 4).根据煤气含焦油量调整二次电压,使电捕焦油器后煤气含焦油量合格。 5).检查电捕排液管及水封是否畅通,及时外排冷凝液,每班清扫一次排液管。 6).稳定煤气含氧量,煤气含氧量超标时及时查明原因消除。 4.冷凝岗位各泵槽正常操作: 1).调整循环氨水泵泵压,使焦炉集气管氨水喷洒压力保持在 0.2~0.25MPa,高压氨水泵定期启动,压力能满足集气管清扫要求。 2).保证各槽的液位正常,不溢槽,不抽空。 3).按时巡查设备运行情况,检查各泵的润滑情况,要求视镜2/3. 4).调整剩余氨水泵流量,使其与氨水处理岗位处理量适合。 5).按时排放沉积在各氨水槽底部的焦油,保证外供氨水不带焦油。 6).检查机械化氨水澄清槽刮板机的运行情况,减速机的油质油量,出渣情况及时运走油渣。 7).调节机槽油水界面,及时调油,保证焦油不带水,氨水不带油。 8).检查废液收集槽,凝结水槽液位及时外送。 9).检查尾气洗净塔运行情况,洗净液喷洒效果,定期外排废水,补充新鲜循环水,确保洗涤效果。 10).焦油槽脱水,蒸汽加热保温使焦油符合要求,焦油的输送管道,在输送前后都必须用蒸汽吹扫干净。 ㈡.开、停车及倒换操作: ⑴.初冷器的开、停、倒换操作: 1.开初冷器: 1).检查各阀门的严密情况,确保其灵活好用。 2).检查上、下段的冷却水系统供水是否正常。 3).各水封槽已注满水,各处仪表齐全完好。 4).打开欲开初冷器的上、下段排液管阀门,用蒸汽吹扫确保畅通。 5).打开初冷器顶部放散,打开通入器体的蒸汽(或氮气)阀门,通入蒸汽(或氮气),待放散冒出大部分蒸汽(或氮气)后,取样做含氧分析合格后,关小蒸汽(或氮气)。 6).煤气系统运行正常后,按离心泵的启动操作步骤启动上、下段冷凝液喷洒泵,调节泵压、循环量,使系统形成循环。 7).打开上段循环冷却水,入口阀门,慢慢打开初冷器出口阀。 8).打开煤气入口阀通煤气,同时关闭蒸汽(或氮气)阀,关闭放散。 9).煤气走通后,根据煤气温度情况开下段冷却水上水阀出口阀,调节冷却水量,使初冷器后煤气温度符合要求。 2.停初冷器: 1).关闭煤气进出口阀门。 2).依次关闭循环水,制冷水入口阀门,并将各段冷却水放空。 3).关闭冷凝液循环喷洒泵出口阀,停上、下段喷洒泵,并将管道内冷凝液放空,并用蒸汽吹扫冷凝液管。 4).打开顶部放散,打开蒸汽管道阀,赶初冷器内煤气,待放散冒出大量蒸汽后,关闭蒸汽,关闭放散,待冷却后放净器内冷凝液,初冷器通入氮气处于备用状态。 3.倒初冷器: 1).按开工操作开待用初冷器。 2).正常后,关闭停用初冷器煤气进出口阀门,关闭冷却水进出口阀门,并放掉系统积液,清扫做为备用或进行检修。 3).调整运行初冷器冷却水量,使温度符合要求。 4).启动运行初冷器的冷凝液喷洒系统。 4.热氨水冲洗运行初冷器: 1).初冷器阻力>1000Pa时,初冷后煤气温度不符合要求,需清扫。 2).打开循环氨水泵至初冷器的氨水管阀门,停上段冷凝液喷洒泵。 3).打开入初冷器的上段氨水阀,对初冷器进行热氨水喷洒清洗。 4).注意煤气温度变化,及时调节冷却水量。 5).清扫完毕后,关闭氨水阀,启动上段冷凝液喷洒泵。 ⑵.电捕焦油器的开停、倒换操作: 1. 开电捕焦油器: 1).电捕水封槽已注满水,确认下液管畅通,各阀门处于关闭状态。 2).电器仪表经检查处于正常状态,绝缘箱通蒸汽加热达到90~ 110℃.使其达到技术指标。 3).做电捕空投试验正常,电工确认绝缘和电气部分的绝缘电阻合格。 4).打开放散管,向电捕内通蒸汽(或氮气),待放散冒出大量蒸汽(或氮气),做含氧量分析合格后,关小蒸汽(或氮气)阀门,使其保持微正压。 5).打开氮气进绝缘箱管道上阀门,调节氮气压力,流量符合规定。 6).关闭放散管和蒸汽阀门,送煤气,打开煤气出、入口阀门(入口快,出口慢)。 7).向电捕送电,逐级升压至规定值,注意电捕二次电压,电流变化。 8).打开下液管阀门,检查退液管排液是否畅通,做好记录。 2.停电捕焦油器操作: 1).按电捕操作要求逐渐由高档降至抵挡,电捕操作电压降至0,切断电源,把三点开关转为接地、放电。 2).打开电捕旁通阀,关闭煤气出、入口阀,使煤气走旁通。 3).关闭电捕绝缘箱,馈电箱氮气保护阀。 4).用蒸汽清扫排液管,保证排液管畅通。 5).用热氨水冲洗电捕沉降,或打开电捕顶部放管,用蒸汽吹扫电捕,赶净器内煤气。 6).清扫完毕,当电捕内温度降至<60℃时,关闭蒸汽放散管,通入少量氮气保压备用。 7).放净器内积液,关闭退液管,关闭绝缘箱加热系统。 3.倒换电捕焦油器操作: 1).按开工操作要求开启用电捕。 2).启用电捕运行正常后,停需停电捕,切断电源,确认接地放电。 3).关闭停电捕进出口阀门,清扫器体,放净器内冷凝液,关闭绝缘箱加热系统,使其处于备用状态。 4.电捕焦油器的清扫: ⑴.蒸汽清扫: 1).按电捕焦油器的停工步骤停电,接地放电,停绝缘箱、蒸汽加热、氮气保护系统,开煤气旁通阀,关闭电捕进出口煤气阀。 2).打开顶部放散,通蒸汽清扫30min. 3).打开氮气管阀,关闭蒸汽,待电捕冷却至常温后,关闭氮气,关闭放散,按开工步骤启动电捕。 ⑵.氨水清扫: 1).电捕焦油断电接地放电。 2).煤气走旁通,关闭煤气出入口阀。 3).打开电捕热氨水清扫管道阀向电捕通热氨水,清扫。 4).清洗完毕后,打开电捕出、入口阀,关闭旁通阀,按电捕开工程序通电开工。 ⑶.鼓风机的开、停、倒换操作: 1. 鼓风机的开机操作: 1).准备好听音棒、测震仪、温度计、压力表及记录本。 2).检查电器线路、仪表、绝缘等机械状况良好。 3).检查油站油位、油温、油路阀门开闭情况是否合乎技术规定,液力偶合器油位是否正常。 4).电工、仪表工、检修工、操作工等相关人员全部到位,准备就绪。 5).启动润滑油泵,备用油泵调为自动,调整油压、油温,观察回油情况是否正常。 6).清扫机体及风机前后排液管,确保畅通,水封槽液位正常。 7).盘车,并上好风机端盖。 8).打开机体下排液管的蒸汽阀门,向机体通蒸汽暖机,机体温度达到60℃~70℃时,关蒸汽,排净机体冷凝液。 9).关闭机体排液管及机前机后排液管阀门。 10).打开风机煤气入口阀~2/3,活动出口阀,大循环管阀开~ 1/2,偶合器调节先打至手动。 11).通知变电所送高压电,通知焦炉地下室等相关单位,准备开机。 12)接上级主管下达指令,启动电机。. 13).手动调节偶合器执行机构,启动输出轴低速运行,观察各处油温、油压、回油,各设备的轴承温度,设备本体温度等是否正常。 14).调整风机的进出口阀门开度。 15).根据煤气量的变化,慢慢提升风机转速,当接近临界转速时,快调偶合器使风机快速越过临界区。 16).首次开工时,由于煤气量较少,为了保证集气管压力稳定和鼓风机正常运行,应以大循环管来进行调节,此后随煤气量的增大逐渐关小大循环,直至完全关闭。根据焦炉集气管压力的变化由液力偶合器调节。 17).当油站油温到38~40℃时开大冷却器冷却水,偶合器油温至55~58℃时,开大冷却器冷却水,使油温符合要求。 18).当风机运行稳定后,打开风机机体及负压等各处排液管阀门排液,确保排液畅通。 19).当风机运行稳定后,与焦炉上升管,地下室联系,把鼓风机液力偶合器执行器由手动切换为自动(焦炉π型翻板,地下室翻板自动)。 20).鼓风机运行正常后转入正常生产,及时巡检,查看各项指标是否符合要求,做好相关记录。 2.鼓风机的停机操作: 1).与各级主管,变电所,焦炉等有关单位联系,共同做好停机、 停煤气准备。 2).接上级主管停机指令后,将偶合器调节由自动转为手动,手动 缓慢降低偶合器输出转速(当快降到临界转速时,快调执行器,使风机转速能够快速降到临界转速以下),同时慢关煤气出口阀。 3).待风机转速降至0时,关闭煤气进出口阀门,切断电机,停主电机。 4).通蒸汽清扫风机机体和各冷凝液排液管,同时进行盘车,把转 子上的附焦油清扫干净,清扫完毕后停汽,凉机,放掉冷凝液。 5).各处轴承温度降至40℃时,油站油温降至30℃时,关闭油冷却器冷却水,停油站油泵。 6).停车后半小时盘车一次,待机体及轴承温度降至常温后每班盘车一次。 7).长时间停机,应将冷却器内液体放空,防止冬季冻坏设备。 3.鼓风机的倒机操作: 1).倒机操作前应先与相关单位联系好,通知相关岗位做好倒机准备。 2).做好准开机的准备工作,偶合器调节切换为手动,开准开风机进口约2/3,活动出口,在主管领导的指挥下,按开机的操作步骤启动准开风机电机。 3).启动准开风机主电机手动调节缓慢提升准开风机的转速,慢慢开出口阀门,同时逐渐降低停风机的转速,慢慢关小停风机的出口阀门,使其平衡,保证焦炉、集气管压力稳定。 4).至待停机的转速降至0时,关闭煤气出、入口阀,同时准开风机的进出口阀开度正常,转速调至正常转速。 5).停风机按停机后操作做为备用。 ⑷、排气洗净塔操作: 1. 开工操作: 1).向尾气液封槽注满水。 2).从洗净塔上部向塔内注入来自管道的循环水,使塔底水位达到液位显示2/3处,关闭循环水注水阀。 3).打开排气洗净泵循环管路上的阀门,开通循环管线。 4).按离心泵的启动步骤启动排气洗净泵形成循环,并调节循环喷洒量,符合排气洗净要求。 5).打开排气风机入口阀,启动排气风机,把各储槽放散排气送入洗净塔。 6).待排气洗涤循环正常后,适当打开送生化处理装置阀门,适量排出洗涤废水送生化处理,并打开新鲜循环水注水阀,保持塔 底液位稳定。 2.停工操作: 1).关闭排气风机的入口阀门,停排气风机。 2).关闭循环水注水阀。 3).停洗涤泵后,将泵体及管道内液体放净。 4).放净塔内洗涤液。 ⑸.机械化澄清槽的开工操作: 1.开工操作: 1).与电工联系,检查电器设备的状况。 2).清理器内杂物,钳工确认刮板机运行和液位调节器装置正常。 3).打开澄清槽的氨水出口,混合液入口阀,待液体充满后,给电启动刮板机。 4).待机械化氨水澄清槽内焦油液位达到~1.7m时,打开焦油出口管道,调节液位调节器,保持机槽焦油、氨水界面稳定。 2.停工操作: 1).关闭冷凝液入口阀和氨水出口阀。 2).将槽内焦油压空,停止刮板机。 3).将槽内液体放净。 ⑹.离心泵的开、停、倒换操作: 1.离心泵的开启流程: 提前检查泵箱油位正常,仪表、电器、贮槽液位正常,阀门灵活好用,管道畅通,准备工作做好。 注:焦油泵需用蒸汽清扫泵前后管道,冬季还需预热油泵至盘车灵活。 2.离心泵的停车流程: 注:焦油泵停泵后需用蒸汽吹扫泵体,泵前后管道,防止堵塞。 3.离心泵的倒泵流程: ㈢、特殊操作: 1.鼓风机部分: ⑴ .突然停电: 停高压电: 1).迅速关闭煤气出口阀门,主电机开关打至停机位置。 2).液力偶合器调节由自动转换为手动,调节执行机构归零。 3).关闭煤气入口阀门,吹扫机体及各下液管。 4).与相关部门联系,询问停电原因,做好记录,做好来电后开 车准备。 停低压电: 若油站油泵未停,不影响风机运行,坚持生产,通知有关领导,联系有关部门尽快供电。若风机因低压控制电路停电造成停机时,按停机处理。 ⑵.突然停水: 油冷却器启用另一路水,坚持生产,通知有关领导。 通知有关部门,尽快恢复供水,若两路水都停,机组轴瓦温 度超过规定值后,且水还没有供给,立即停车。做好供水恢复后,开车准备。 ⑶.突然停蒸汽: 询问相关部分原因,尽快恢复,以便于吹扫排液管。 ⑷.遇到下列情况之一鼓风机司机有权紧急停机: 1).机组突然发生强烈振动或机体内有磨刮声时; 2).任一轴承或密封处发生冒烟时; 3).进油管路上油压下降至0.08MPa,而连锁辅助油泵投入工作后,油压仍低于0.05MPa时; 4).轴承温度急剧升高到75℃以上,采用各种措施仍不能下降时; 5).鼓风机转子的轴向位移大于0.5㎜,采用各种措施后轴向位移继续增大时; 6).风机前煤气管道着火时; 7).油箱的油位下降至最低油位线,加入新油,油位仍继续下降且得不到控制时; 2.电捕焦油器部分: ⑴.突然停电: 立即拉下电捕电闸,接地放电,并向上级主管汇报,做好来 电后开工准备,做好记录,询问停电原因送电时间,若停电时间较长则按停工处理。 ⑵.突然停汽: 注意电捕绝缘箱温度,当绝缘箱温度低于80℃时,停电捕 供电,询问停汽原因,恢复供冷时间,做好记录,做好送汽后开车准备。 3.初冷器部分: ⑴ .突然停循环水: 短时停水,增大初冷器制冷水量,控制器后煤气温度﹤30℃, 长时间停水,将备用初冷器投入,增加冷却水量维护生产,询问停水原因及恢复供水时间,做好记录。 ⑵ .突然停制冷水: 短时停水,增大初冷器循环水量,控制器后煤气温度﹤ 30℃,长时间停水,使用备用初冷器,增大循环水量维护生产,询问停水原因及恢复供水时间,做好恢复供水正常生产操作准备。 ⑶ .突然停循环水,制冷水两路水: 两路水都停后,直接停产,询问停水原因供水时间,做好 供水后开工准备。 4.冷凝岗位部分: ⑴.突然停电: 切断所有运行泵的电机电源,并关闭出口阀门,与相关部门联系,若短时恢复供电,做好准备;若停电时间长,按停泵操作,注意各槽液位变化,控制好各槽不满流。 焦油泵在正常送油时发生停电,立即切断电源,关闭出口阀门;若停电时间长,需用蒸汽吹扫送油管道。 ⑵.突然停冷却水 与综合供水泵房联系,询问停水原因及时间,若时间短,坚持生产,加强检查;若时间长,请示有关部门,按停工操作处理。 ⑶.突然停仪表风: 将自控调节阀门前后阀门关闭,打开旁通阀,用旁通阀人工 手动调节维护生产,来风后,关闭旁通阀,打开调节阀前后阀门,恢复调节自控做好记录。 注:冷鼓工段全部停电,送电后,首先必须先将循环氨水泵启动,循环正常后,再将风机开启,之后依次启动其它设备。 六.岗位安全规则: 1.对高压电机的开停,严格执行操作制度。 2.禁止吸烟,严禁将火种带入本岗位。 3.劳保用品必须穿戴齐全方可进入操作岗位进行操作,不许穿铁钉、铁掌鞋,进入化产区。 4.检查有气液体溢出槽罐设备时,要求站在上风侧,手扶牢栏杆。 5.在风机房和煤气设施上检修时,严禁使用铁制工具拷打,应用铜 制工具。 6.电捕焦油器运行状态下,禁止上电捕焦油器,停电检修时,必须先断电,接地放电,防止电捕内残余静电击伤。 7.需进入设备、罐、槽、塔内检查,检修时,必须清扫后做气体分析试验合格后方可进入。人孔全部打开,保持通风,进入煤气设备时,必须将煤气进出口堵上盲板。 8.检查电机、风机轴承,各泵轴承温度情况时,以手背面触摸,禁用掌心。 9.开关高处阀门,至少2人配合操作,固定好扶梯,防止跌滑。 10.装焦油及取样时,要站在一侧,防止热油溅出烫伤。 11.出现煤气泄露时,应首先通风散气,预防发生中毒和爆炸事故。 12.本工段区域内动火检修必须事先办理动火许可证,并确切落实安全措施。 13.电捕初次投用前,本体应进行气密性试验合格后,方可投入使用。 14.第一次启动电气设备不成功,必须通知专业维护人员进行检修处理后,方可再次送电,50KW以上电机严禁连续启动三次。 15.电捕焦油器绝缘箱通氮气保护,发现氮气异常时,应立即断电。 16.电捕焦油器煤气含氧分析仪报警,联锁自动跳闸后,需查明原因,进行有效处理后,方可重新投入使用。 17.操作室,操作台等设备不准有明线,发现漏电现象及时通知电工处理,清除隐患。 18.发现有跑、冒、滴、漏现象,及时通知相关人员处理。 19.保证电机运行平稳,各项指标符合要求,发现异常,及时处理。 20.各运行设备联轴器无防护罩,禁止运行。 七.设备维护生产保养规程: ㈠.设备概要: 1.非标设备: ⑴ .初冷器A、B、C: 3台 长×宽×高:4484×3300×~32866 F总=5144㎡ 上段:F=3026㎡ 壳程:焦炉煤气~-0.001MPa(表) 管程:循环水0.4MPa(表)30~40℃ 换热管:57×3×4500 n=3800 下段:F=2118㎡ 壳程:焦炉煤气~-0.002MPa(表) 管程:制冷水0.4MPa(表)16~23℃ 换热管:57×3×4500 n=2660 ⑵.气液分离器:1台 2400×7315 V总=24m3 介质:焦炉煤气、氨水、焦油 温度:~80℃ 压力:~-0.001MPa(表) ⑶ .机械化氨水澄清槽:2台 型号:71.067 长×宽×高:24616×4590×~5686 V全=340m3 介质:焦油、氨水、焦油渣 温度:~80℃ 压力:常压 附传动装置:电动机直联型三级卧式行星摆线针轮减速机 型号:XWSD2.2-1174-1/16555 电动机:电压:380V 功率:N=2.2KW 转速:1430r/min 总减速比:i=16555×2.5238=41781.5 刮板运输机:工作能力:~400kg/h焦油渣 工作速度:3.7555m/h ⑷.循环氨水槽:2台 8000×5100 V总=256m3 立式 温度:~80℃ 压力:常压 ⑸.剩余氨水槽:2台 8250×8600 V全=460m3 立式 介质:氨水、水蒸汽及冷凝液 温度:~80℃ 压力:常压 附加热装置:加热蛇管:57×3.5 F=40.8㎡ 管内温度:~158℃ 管内压力:~0.5MPa ⑹.焦油中间槽:1台 5200×4500 V总=95.6m3 立式 介质:焦油、水蒸汽及冷凝液 温度:~80℃ 压力:常压 附加热装置:加热蛇管:57×3.5 F=~12㎡ 管内温度:~158℃ 管内压力:~0.5MPa ⑺.焦油槽:2台 8800×8200 V总=500m3 立式 介质:焦油、水蒸汽及冷凝液 温度:~75℃ 压力:常压 附加热装置:加热蛇管:57×3.5 F=48㎡ 管内温度:~158℃ 管内压力:~0.5MPa ⑻.初冷器水封槽:6台 800×3000 V总=1.5m3 立式平顶 介质:煤气冷凝液 温度:20~45℃ 压力:常压 ⑼.鼓风机水封槽:1台 长×宽×高=2600×1000×4000 V全=10.4m3 立式平顶 介质:煤气冷凝液 温度:~35℃ 压力:常压 ⑽.鼓风机水封槽:1台 长×宽×高=2600×1000×4000 V 介质:煤气冷凝液 温度:~35℃ 压力:常压 ⑾.电捕水封槽:1台 长×宽×高=2600×1000×4000 V 介质:电捕液 温度:~35℃ 压力:常压 ⑿.凝结水槽:1台 3000×2500 V总=18m3 介质:蒸汽冷凝液 温度:~90℃ 压力:常压 ⒀.废液收集槽:1台 4000×4000 V总=50m3 介质:焦油、氨水 温度:~75℃ 压力:常压 3 全=10.4m3 全=10.4m立式锥顶 立式平顶 立式平顶 立式平顶 ⒁.上段冷凝液循环槽:1台 2200 L=6000 V全=21.3m3 卧式 介质:煤气冷凝液 温度:~45℃ 压力:常压 ⒂.下段冷凝液循环槽:1台 2200 L=6000 V全=21.3m3 卧式 介质:煤气冷凝液 温度:~45℃ 压力:常压 ⒃.尾气液封槽:1台 400×600 V总=0.075m3 立式平顶 介质:焦油、氨水 温度:常温 压力:常压 ⒄.排气洗净塔:1台 1500×~17720 V总=23.6m3 立式平顶 介质:槽区尾气、循环水 温度:~40℃ 压力:常压 丙装聚丙烯花环填料 25×9乱堆 2. 标准设备 ⑴.离心鼓风机:2台 型号:D1450-1.11/0.81 Q=1450m3/h △P=30000Pa 输送介质:焦炉煤气 介质重度:~0.45㎏/m3 进口压力:~-3500~-5000Pa 进口温度:22~25℃ 转速:4340r/min 轴功率:936KW 附:电机 功率:1000KW 电压:10KV 2台 附:防爆调速型液力偶合器(配套板式冷却器) 2台 附:润滑油系统(含防爆油站,高位油箱等) 2台 附:变速器 2台 ⑵.排风机:2台 型号:9-19NO.4A2右90 Q=970m3/h △P=3665Pa 输送介质:含氨尾气 附电机 功率:2.2KW 电压:380V 型号:YB90L-2W ⑶.循环氨水泵:2台 型号:350S-75B Q=828~1225m3/h H=59~47.5m 单级,双吸中开式离心泵 输送介质:氨水 介质重度:~1000㎏/m3 温度:~75℃ 转速:1470r/min 附电机 功率:250KW 电压:10KV 型号:Y450-4C 2台 ⑷.剩余氨水泵:2台 型号:IS65-40-250 Q=15~30m3/h H=82~78m 单级,单吸式离心泵 输送介质:氨水 温度:~75℃ 转速:2900r/min 附电机 功率:15KW 电压:380KV 型号:Y132S2-2 2台 ⑸.焦油泵:2台 型号:80AY-60 Q=50m3/h H=60m 单级,单吸式离心泵 输送介质:焦油 温度:~80℃ 转速:2950r/min 附电机 功率:18.5KW 电压:380KV 型号:Y160L-2 2台 ⑹.上段冷凝液循环泵:2台 型号:IS100-65-200 Q=60~120m3/h H=54~47m 单级,单吸式离心泵 介质:煤气冷凝液 温度:~45℃ 转速:2900r/min 附电机 功率:22KW 电压:380KV 型号:YB180M-2W 2台 ⑺.下段冷凝液循环泵:2台 型号:IS150-125-315 Q=120~240m3/h H=34~29m 单级,单吸式离心泵 介质:煤气冷凝液 温度:~30℃ 转速:1450r/min 附电机 功率:30KW 电压:380KV 型号:YB200L-4W 2台 ⑻.凝结水泵:2台 型号:ISR50-32-200 Q=7.5~15m3/h H=48~52.5m 单级,单吸式离心泵 介质:氨水 温度:~75℃ 转速:2900r/min 附电机 功率:5.5KW 电压:380KV 型号:Y132S1-2 2台 ⑼.鼓风机水封槽液下泵:2台 型号:LYA40-160 Q=28m3/h H=28m 单级,单吸式耐腐蚀液下泵 介质:煤气冷凝液、焦油、氨水 温度:~30℃ 转速:2960r/min 插入深度:L=3800㎜ 附电机 功率:7.5KW 电压:380KV 型号:YB132S2-2W 2台 ⑽.废液收集槽液下泵:2台 型号:LYA40-160 Q=28m3/h H=28m 单级,单吸式耐腐蚀液下泵 介质:煤气冷凝液 温度:~50℃ 转速:2960r/min 插入深度:L=3800㎜ 附电机 功率:7.5KW 电压:380KV 型号:YB132S2-2 2台 ⑾.电捕水封槽液下泵:1台 型号:LYA40-160 Q=28m3/h H=28m 单级,单吸式耐腐蚀液下泵 介质:煤气冷凝液 温度:~30℃ 转速:2960r/min 插入深度:L=3800㎜ 附电机 功率:7.5KW 电压:380KV 型号:YB132S2-2W 1台 ⑿.排气洗净泵:2台 型号:IS50-32-200 Q=7.5~15m3/h H=52.5~48m 单级,单吸式离心泵 输送介质:氨水 温度:~75℃ 转速:2900r/min 附电机 功率:5.5KW 电压:380KV 型号:Y132S1-2 2台 ⒀.高压氨水泵:2台 型号:D46-50×7 Q=30~55m3/h H=388.5~322m 多级,单吸式离心泵 输送介质:氨水 温度:~75℃ 转速:2950r/min 附电机 功率:75KW 电压:380KV 型号:Y280S-2 2台 ⒁.手动单梁起重机:1台 型号:SDQ-10 起重量:10吨 LK=13米 起升高度:6米 轨宽:70㎜ 附:手拉葫芦 起重量:10吨 起升高度:10米 型号:HS10 1台 ⒂.手动单轨小车:1台 型号:SDX-5 起重量:5吨 起升高度:5米 附:手拉葫芦:起重量:5吨 起升高度:5米 型号:HS5 1⒃.带斗小推车:3台 ⒄.滤油机:1台 型号:LY150 配电机:功率:3KW 电压:380V ⒅.电捕焦油器:2台 型号:FD248-II-A(D) 工作介质:含焦油、萘雾滴的焦炉煤气 处理煤气量:48000~58000m3/h 煤气温度:22~25℃ 煤气压力:~-3~-5KPa 绝缘箱夹套蒸汽压力:0.4~0.5 MPa 蒸汽加热管压力:0.4~0.5 MPa 顶部清洗液压力:﹥0.3 MPa 沉淀极: 结构型式:蜂窝式 单管规格:正六边形内切圆:250×4500 台 有效截面积:13.4㎡ 附:高压恒流电源(户内型)1.0A/60KV 2台 ㈡.设备维护保养: 1. 操作人员必须做到“四懂四会”:懂结构、懂原理、懂性能、懂用途、会使用、会维护保养、会排除故障,会小修。 2. 操作人员要精心操作正确使用设备,严格执行操作规程。 3. 严格控制工艺技术条件,做到不超温、不超压、不超负荷。 4. 经常巡检各运行设备的润滑油系统,保证油位合乎要求。 5. 各阀门要定期加油,保证灵活好用。 6. 备用运转设备每班盘车一次,备用风机每班盘车1/4. 7. 各运行设备在启动前首先盘车,并查看附属设备及各处润滑情况,存在缺陷的设备严禁投入运行。 8. 风机油箱润滑油定期取样化验,油质有变化时及时处理,每月滤油一次,定期清洗滤芯。 9. 定期化验液力偶合器油箱油质,不合格时必须及时更换。 10.备用电动鼓风机每月做空投试验一次,由电工检查绝缘情况二次,并要求电工在交接本上做好记录。 11.风机运行周期为3个月,到期要由检修人员进行全面检查、测试,确定能否继续运行,并将备用风机进行检查保养。 12.电捕焦油器氨水喷头每年清扫一次,更换堵塞喷嘴。 13.让电器人员经常检查电捕电器系统绝缘性能。 14.正常情况下,氨水泵3各月倒换一次,进行全面检查。 15.50KW以上的电机严禁连续启动三次。 16.所有设备和环境做到卫生清洁,无跑、冒、滴、漏现象,做到文明生产。 17.设备定期刷漆,防腐,提前做好设备夏季降温,冬季防冻工作。 18.设备冷却水及冷却器冷却水水温,水压及时检查调节,防止水温过高损坏设备和油中串水。 19.严格执行巡回检查制度,实行“听、摸、查、看、闻”五字方针,发现异常及时处理。 (一) 饱和器法硫酸铵生产工艺流程 1. 鼓泡式饱和法 由鼓风机来的焦炉煤气,经电捕焦油器后进入煤气预热器。在预热器内用间接蒸汽加热煤气到 60~70℃或更高的温度,目的是为了使煤气进入鼓泡式饱和器蒸发饱和器内多余的水分,保持饱和器内的水平衡。预热后的煤气沿饱和器中央煤气管进入饱和器,经泡沸伞从酸性母液中鼓泡而出,同时煤气中的氨被硫酸所吸收。煤气出饱和器后进入除酸器,捕集其夹带的酸雾后,被送往粗苯工段。 鼓泡式饱和器后煤气含氨一般小于 0.03g/m3。冷凝工段的剩余氨水经蒸氨后得到的氨气,在不生产吡啶时,直接进入饱和器;当生产吡啶时将此氨气通入吡啶中和器。氨在中和器内与母液中的游离酸及硫酸吡啶作用,生成硫酸铵,又随中和器回流母液返回饱和器。饱和器母液中不断有硫酸铵生成,在硫酸铵含量高于其溶解度时,就析出结晶,并沉淀于饱和器底部。其底部结晶被抽送到结晶槽,在结晶槽内使结晶长大并沉淀于底部。结晶槽底部硫酸铵结晶放到离心机内进行离心分离,滤除母液,并用热水洗涤结晶,以减少硫酸铵表面上的游离酸和杂质。离心分离的母液与结晶槽满流出的母液一同自流回饱和器中。从离心机分离出的硫酸铵结晶经螺旋输送机,送入沸腾干燥器内,用热空气干燥后送入硫酸氨储斗,经称量包装入成品库。 为了使饱和器内煤气与母液接触充分,必须使煤气泡沸伞在母液中有一定的液封高度,并保证饱和器内液面稳定,为此在饱和器上还设有满流口,从满流口溢出的母液经插入液封内的满流管流入满流槽,以防止煤气逸出。满流槽下部与循环泵链接,将母液不断地抽送到饱和器底部的喷射器。因而一定的喷射速度,故饱和器内母液被不断循环搅动,以改善结晶过程。煤气带入饱和器的煤焦油雾,在饱和器内与硫酸作用生成所谓的酸煤焦油,泡沫状酸煤焦油漂浮在母液面上,并与母液一起流入满流槽。漂浮于满流槽液面上的酸煤焦油应及时捞出,或引入一分离处理装置与母液分离,以回收母液。饱和器内所需补充的硫酸,由硫酸仓库送至高置槽,再自流入饱和器,正常生产时,应保持母液酸度为 4%~6%,硫酸加入量为中氨的需要量;当不生产粗轻吡啶时,硫酸加入量要大一些,还要中和随氨气进入饱和器的氨。饱和器在操作一定时间后,由于结晶的沉积将使其阻力增加,严重时会造成饱和器的堵塞。所以操作中必须定期进行酸洗和水洗。当定期大加酸、补水、用水冲洗饱和器及除酸器时,所形成的大量母液有漫流槽满流至母液储槽。在正常 生产时又将这些母液抽回饱和器以作补充。饱和器是周期性连续操作设备,为了防止结晶堵塞,定期大加酸和水洗,从而破坏了结晶生成的正常条件,加之结晶在饱和器底部停留时间短,因而结晶颗粒较小,平均直径在 0.5mm。这些都是鼓泡式饱和器存在的缺点。 2 2 .喷淋式饱和器法 喷淋式饱和器分为上段和下段,上段为吸收室,下段为结晶室。 由脱硫工序来的煤气经煤气预热器预热至 60~70℃或更高温度,目的是为了保持饱和器水平衡。煤气预热后,进入喷淋式饱和器的上段,分成两股沿饱和器水平方向沿环形室做环形流动,每股煤气均经过数个喷头用含游离酸量 3.5%~4%的循环母液喷洒,以吸收煤气中的氨,然后两股煤气汇成一股进入饱和器的后室,用来自小母液循环泵(也称二次喷洒泵)的母液进行二次喷洒,以进一步除 去煤气中的氨。煤气再以切线方向进入饱和器内的除酸器,除去煤气中夹带的酸雾液滴,从上部中心出口管离开饱和器再经捕雾器捕集下煤气中的微量酸雾后到终冷洗苯工段。喷淋式饱和器后煤气含氨一般小于 0.05g/m3。饱和器的上段和下段以降液管联通。喷洒吸收氨后的母液从降液观念流到结晶室的底部,在此结晶核被饱和母液推动向上运动,不断地搅拌母液,使硫酸铵晶核长大,并引起颗粒分级。用结晶泵将其底部的浆液送至结晶槽.含有小颗粒 的母液上升至结晶室的上部,母液循环泵从结晶室上部将母液抽出,送往饱和器上段两组喷洒箱内进行循环喷洒,使母液在上段与下段之间不断循环。饱和器的上段设满流管,保持液面并封住煤气,使煤气不能进入下段。满流管插入漫流槽 7 中也封住煤气,使煤气不能外逸。饱和器满流口溢出的母液流入漫流槽内的液封槽,再溢流到满流槽,然后用小母液泵送至饱和器的后室喷洒。 冲洗和加酸时,母液经漫流槽至母液储槽,再用小母液泵送至饱和器。此外,母液储槽还可供饱和器检修时储存母液之用。结晶槽的浆液经静置分层,底部的结晶排入到离心机,经分离和水洗的硫酸 铵晶体由胶带输送机送至振动式流化床干燥器,并用被空气热风机加热的空气干燥,再经冷风冷却后进入硫酸铵储斗。然后称量、包装送入成品库。离心机滤出的母液与结晶槽满流出来的母液一同自流回饱和器的下段。干燥硫酸铵的尾气经旋风除尘器后由排风机排放至大气。为了保证循环母液一定的酸度,连续丛母液循环泵入口管或满流管处加入质量分数为 90%~93%的浓硫酸,维持正常母液酸度。由油库送来的硫酸送至硫酸储槽,再经硫酸泵抽出送到硫酸高置槽内,然后自流到满流槽。喷淋式饱和器生产硫酸铵工艺,采用的喷流式饱和器,材质为不锈钢,设备使用寿命长,集酸洗吸收、结晶、除酸、蒸发为一体,具有煤气系统阻力小,结晶颗粒较大,平均直径 0.7mm,硫酸铵质量好,工艺流程短,易操作等特点。新建改建焦化厂多采用此工艺回收煤气中的氨。 (二)、影响硫铵结晶粒度因素的控制 焦化厂炼焦煤气中氨的回收,普遍采用饱和器法生产硫铵。由于硫铵结晶过程受多种因素影响,生产中一旦某种因素控制不当,就会造成产品颗粒碎小,水分、酸度超标,影响产品质量。因此,找出影响硫铵结晶粒度的关键因素,寻求最佳操作方法,成为一个重要课题。 1 1 .硫铵结晶原理 硫铵的结晶属于反应过程,主要由反应、过饱和溶液的形成、晶核的产生和晶体的成长几个阶段组成。随着反应的进行,形式过饱和溶液,达到一定过饱和度时,析出固相微观晶粒,这是晶核的形成过程,也称为初级成核,接着是晶核的长大也称为晶体的生长过程。同时,由于晶液的流动,晶体之间及晶体与设备之间的摩擦、碰撞,液体对晶体表面的冲刷,又产生新的晶核,称为二次成核。 通常晶核的形成和晶体的成长是同时进行的。在结晶过程中,无论是晶核的形成,还是晶核的生长,都要消耗溶液中的溶质,均以一定的过饱和度为推动力。每一粒晶体都是由一粒晶核生长而成的,在一定条件下,如果晶核成核速率越大,晶核的生成量越多,溶液中有限的溶质要同时供应大量的晶核生长,晶核的生长速率就越慢,结果导致大量的细小结晶;反之,晶核的生成量越少,结晶粒度就会长得越大。可见,晶核的生成速率和晶核的生长速率是此消彼长的关系,如能控制这两种速率,便可控制结晶的粒度。 此外,结晶条件对产品的粒度也有很大的影响,如温度、搅拌、酸度、杂质等都以一定的方式影响结晶过程。 2. 影响硫铵结晶粒度的因素 根据结晶原理分析,影响硫铵结晶粒度的因素,归纳起来,主要有以下几项: (1)饱和器工作温度 (2)母液的搅拌程度 (3)母液的酸度和加酸制度 (4)母液的晶比 (5)母液中的杂质 生产中对一定工艺条件来说,影响较大的往往是哪些变化频繁,或在量的变化上敏感的因素,并且由于产生的结果滞后而增加了控制上的度。对上述几个因素进行分析可以发现,饱和器工作温度和母液的搅拌程度变动不大,可以说近似恒定;母液的酸度、晶比随时间呈周期性变化,比较频繁,控制不当,对结晶粒度将产生很大影响;母液中的杂质的影响,在量的变化上比较敏感,一般来说带有很大的偶发性,可是一旦发生,对生产的影响很大。所以,母液的酸度、晶比、杂质含量,是生产控制的重点。 (三)、 影响因素的控制 1 3.1 母液酸度 母液酸度对硫铵结晶的影响主要表现在两个方面:一是酸度的高低对结晶形状的影响,二是酸度的频繁变动破坏了结晶的正常生长条件。在一定条件下,随着母液酸度的提高,母液的介稳区减小,硫铵晶形从多面体颗粒转变为细长易碎的六角棱柱形,甚至针状,同时,母液黏度增大,硫铵分子扩散阻力增加,阻碍晶体的正常生长;但是过低也不行,虽然硫铵结晶在 pH5~6 的弱酸性介质中生 成较大的圆形晶体,但是使氨的吸收效率下降,还易造成饱和器堵塞,特别是当母液搅拌不充分或酸度发生波动时,可能在母液中局部出现中性或碱性区,母液中的杂质铁等金属离子和铵生成胶态氢氧化物,并蒙在硫铵晶体上,使晶体成长困难和结晶过程复杂化,而且当母液酸度低于 3.5%时,因母液密度下降易产生泡沫,使饱和器操作恶化。为避免这些影响,必须在酸性介质中进行结晶,正常生产时,母液酸度保持在 4%~6%为宜。酸度对结晶粒度的影响还表现在定期向系统大加酸时,母液酸度大幅度提高,使母液中的晶种消失,破坏了结晶的正常生长条件。再次结晶时,在较高饱和度下发生初级成核,使母液中的细小结晶增多。因此要生产大颗粒结晶硫胺,应减少大加酸的次数,如把每班一次大加酸改为 1~2 天一次,尽量延长饱和期的稳定操作时间。 2 3.2 母液晶比 母液中所含硫胺结晶的体积与母液和结晶总体积的比,称为晶比。对饱和器中晶比的控制,是控制硫胺结晶粒度的重要措施。从结晶原理可以知道,如能控制成核速率和晶核的生长速率便可控制晶体的粒度。然而,在生产中这两种速率是极不易控制的,无论是爆发式的初级成核,还是因摩擦碰撞产生的二次成核都很难控制,生成的晶核总是过量,即成核速率过高。晶核的生长速率相对于成核速率来说是很慢的,在其他条件不变时主要取决于母液的过饱和度,提高过饱和度可以加快晶体的生长。过饱和度的高低,在一定温度下取决于母液中晶核的数量。当母液中存在足量晶核时,新生成的硫胺溶质完全用于晶体的生长,过饱和度趋于稳定,晶体处于稳定的生长环境中。生产中采用控制晶比的办法来控制过饱和度,达到控制晶体粒度的目的。晶比的大小直接影响结晶的粒度。晶比过大时由于摩擦碰撞机会增多,大颗粒结晶被破碎,使二次成核量增大,晶体成长速率减慢,晶体粒度减小,并使母液搅拌阻力增加,导致搅拌不良,同时减少了氨与硫酸反应所需的容积,不利于氨的吸收,还易加重堵塞情况;晶比太小可能出现晶核量少,使过饱和度升高,产生大量的初级成核,使结晶粒度减小,晶比太小,使取出次数增加,缩短了晶体的生长时间,同样使晶体粒度减小。因此,母液中必须控制一定的晶比,以利得到大颗粒硫胺。晶比的控制原则应是:避免初级成核,适当控制二次成核,尽量延长晶体的 生长时间。对晶比的控制,除在量上控制晶比外,还要对结晶的形状、色泽进行观察,预测饱和器内结晶情况,结合实际取出结晶粒度进行判断调节。如果发现晶液中结晶细小,且取出晶粒也小,则应考虑是否酸度过高,还是晶比高低不当,成核过多所致;如果不仅结晶细小而且着色,则应考虑杂质影响。正常生产中晶比的控制,最小不低于 10%,达 30%时取出为宜。 3 3.3 杂质 溶液中的杂质,对结晶过程的所有阶段都产生影响。硫铵母液中杂质的种类和含量,主要取决于所采用的工艺流程、硫酸质量、用水质量和设备的防腐质量。母液中所含的可溶性杂质主要有铁、铝、铜、铅、锑、砷等各种盐类,多半来自硫酸、设备腐蚀和工业用水,这些离子吸附在硫铵结晶的表面,遮盖了结晶表面的活性区域,使结晶成长缓慢;有时由于杂质在一定晶面上的选择性吸附,以致形成细小畸形颗粒。金属离子对硫铵晶体的生长有较大影响,尤其是铁离子影响最大,即使在母液中含量极少,也会使晶体生长速率显著下降。例如三价铁离子会促使介稳区扩大,减慢结晶速度,在溶液中含量达 0.1%时会促使硫铵结晶变长,而在较高浓度时导致生成针状晶体。这种晶体会在生产过程中大量破碎,使成品硫铵的粒度大幅减小。此外,母液中的不溶性杂质如煤焦油雾,有时也会与母液形成稳定的乳浊液附着在晶体表面,阻碍晶体生长。 母液中的杂质不仅影响硫铵的晶形和晶体成长,而且还使单位时间内晶体体积总增长量小于饱和器中硫铵生成量,打破固液平衡,使母液的过饱和度升高,不仅使晶体强度降低,同时形成大量针状晶核,迅速充满溶液中,破坏正常操作。因此,必须在工艺、设备等方面采取有效措施,从根源上减小杂质的进入。 1、粗苯产品及其用途 粗苯是黄色的透明液体,是多种有机化合物的混合物。粗苯本身用途不大,但将粗苯精制加工可得纯苯(C6H6)、甲苯(C6H5CH3)和二甲苯{C6H4(CH3)2等产品。纯苯用于人造纤维、塑料、药物及燃料,甲苯用于制造炸药、合成纤维,二甲苯由于橡胶、油漆的溶剂和航空及内燃机燃料的添加剂。总之,粗苯是一种非常宝贵的化工基本原料。 2、粗苯的组成、性质和质量 2.1粗苯的组成 粗苯的组成波动较大,主要取决于炼焦配煤的组成及炼焦产物在炭化室内热解的程度(及焦炉的炭化温度)粗苯主要组分的平均含量如下: 苯55—80%:甲苯11—22%:二甲苯2—6%:不饱和化合物(如环戊二烯(C5H6)苯乙烯(C6H5CHCH2)等7—12%:硫化物(如二硫化碳(CS2)噻吩(C4H4S)等0.3—1.8%. 2.2粗苯的性质 粗苯比水轻,微溶于水,且易与水分离。在储存较长时间时,由于含有不饱和化合物的氧化和聚合所形成的树脂状物质又溶解于粗苯中,能使粗苯着色变为暗褐色(或淡红色)。粗苯易燃,闪点为12℃.粗苯蒸汽在空气中的体积浓度为1.4%-7.5%时,能形成爆炸性混合物。若粗苯着火时,应使用泡沫剂或蒸汽灭火。粗苯在管道内流动时极易产生静电,为防止引起静电火花的危险,所以粗苯生产及产品运输和储存设备与管道应安装有可靠接地导电装置。 2.3粗苯的质量及其指标 粗苯的各主要组分均在180℃前馏出,180℃后的流出量当作100%来计算,故以其180℃前的馏出量作为鉴别粗苯质量的指标之一。粗苯在180℃前的馏出量取决于粗苯工段的工艺流程和操作制度。180℃前馏出量愈多,粗苯质量愈好。一般要求粗苯的180℃前馏出量为91%—93%粗苯的质量指标如下表。 指标名称 加工用粗苯 溶剂用粗苯 外观 黄色透明液体 馏程%75℃前馏出量(V) 180℃前馏出量(W) 密度(20℃),g/ml ≥93 0.871-0.900 ≤3 ≥91 ≤0.900 水分 室温(18-25℃)下目测无可见不溶解的水 3.粗苯生产产量的估算 3.1粗苯产率 粗苯产率与装炉煤的质量、炼焦温度和焦炉炉顶可见温度有关,随装炉煤挥发分的提高而增加,随炼焦温度、炉顶可见温度的提高而下降。 粗苯产率可按以下经验公式进行计算:(1)y=a+bv 式中:y——粗苯产率(对于煤)% V——炼焦用煤的可燃基挥发分,% a、b——常数 常数a、b因各厂的装炉煤性质和主要工艺条件的不同而异。在一定的条件下a和b是定值。以某焦化厂为例:a=-0.64,b=0.065(适用范围:v=27.96—30.37%,y=0.0988—1.37%)) 2、y=-1.6+0.144v-0.0016(v)2 式中符号代表意义同上(v在20—30%之间)。 粗苯产率一般为炼焦干基配合煤的0.75%—1.1%,即用炼焦洗精煤炼焦时,没用一顿干煤,可得到7.5—11公斤粗苯。焦炉煤气中一般含粗苯为25—40g/m3. 3.2粗苯产量的估算 (1)基础数据(举例) 焦炉用煤量(平均) 50t/h(干基) 净煤气产率 320—330Nm3/t干煤,取值325 m3/t 洗苯塔前煤气含苯量 28g/m3 洗苯塔后煤气含苯量 3g/m3 粗苯产量(对干煤) 0.82% (2)粗苯产量 a.按煤气中含苯量进行估算(实际生产中煤气含苯量可由化验分析得到): 50*325*(28-3)/1000=406.25kg 即每天可生产粗苯10吨左右。 b.按粗苯产率进行估算: 50*0.0082*1000=410kg/h 即每天可生产粗苯约10吨左右。 4.粗苯生产消耗洗油、蒸汽、焦炉煤气的指标 (1)洗油<100kg/t粗苯(国内有些焦化厂<70kg/t粗苯); (2)蒸汽10-1.5t/t粗苯; (3)焦炉煤气450-550m3/t粗苯。 5.洗油吸收粗苯的基本原理 用洗油吸收焦炉煤气中的粗苯是物理吸收过程,服从亨利定律和道尔顿气体分压定律。当煤气中粗苯蒸汽分压大于洗油液面上粗苯蒸汽压时,煤气中粗苯被洗油吸收。 6.从焦炉煤气中回收粗苯的方法 (1)吸收粗苯部分 a.洗油吸收法(本公司采用):用洗油在专门的洗涤塔内吸收焦炉煤气中的粗苯,将吸收了粗苯的洗油(称为富油)送至脱苯塔蒸馏装置中,在此粗苯被提取出来,脱苯后的洗油(称为贫油)经冷却后重新送回(循环)洗涤塔内吸收粗苯。 b.吸附法(如果用活性碳做吸附煤气中的粗苯,作为煤气含苯化验分析方法之一) c.低温加压法 (2)蒸馏脱苯部分 吸收了煤气中粗苯的洗油称为富油。按富油加热发生分为: a. 预热器加热富油(用水蒸气做热源)的脱苯法。 b. 管式炉加热富油(用焦炉煤气做主要热源)的脱苯方法。 7.从富油中蒸出粗苯的原理 从富油中蒸出粗苯是根据洗油和粗苯两者沸点2的不同,虽然粗苯沸点小于180℃,但其液体混合物又不具有恒沸点,同时洗油又是此混合物中主要组份,因此混合物的沸点介于粗苯和洗油沸点(230-300℃)之间,并趋近洗油的沸点,于是采用降低蒸馏温度的水蒸气蒸馏方法。 8.粗苯工段工艺简介及流程图 8.1工艺简介 从硫铵工段来的煤气进入终冷塔,在此被冷却至25-28℃后,由塔底进入洗苯塔,在塔内与塔顶下来的洗油(贫油)逆流接触后,煤气中的苯族烃被洗油贫油吸收下来,从塔顶出来的煤气一部分回焦炉加热。其余部分送至气柜等用户。 吸收苯族烃的贫油变为富油后,在洗苯塔底进小富油泵送至富油槽。在由大富油泵送至蒸苯部分处理。脱苯后的热贫油经一段贫富油换热器后进入脱苯塔底部热贫油槽中,然后用贫油泵从槽中抽出经二段贫富油换热器后,一段贫油冷却器,二段贫油冷却器冷却后送往洗苯塔顶喜欢喷洒适用。 由洗苯塔的富油经泵送入油气换热器与脱苯塔顶的苯蒸汽换热后进入二段、一段贫油换热器与来自脱苯塔的热贫油换热后进入管式炉的对流段和辐射段将富油加热至180±5℃后进入脱苯塔蒸馏,其中1-2%左右富油进入再生器,用过热蒸汽蒸吹,再生器顶部蒸出的气体进入脱苯塔,下部排出的残渣流入残渣槽。 脱苯塔出来的苯蒸汽进入冷凝冷却器,先与富油换热器后进入油水分离器,粗苯流入回流柱,部分用回流泵送脱苯塔顶做回流,其余流入粗苯中间槽,定期用产品泵送往苯库。 油水分离器分离水流入控制分离器进一步油水分离粗苯流入中间槽,水去放空槽进行处理。 8.2粗苯工段工艺流程图(间附页) 9.粗苯工段主要生产工艺设备概况 (1)煤气横管终冷器(F=3100m2)2台(一开一备),设计处理焦炉煤气量33740m3/h,顶部和中部设有循环喷洒冷凝液装置,以机械性的冲洗和吸附终冷器内横管壁上附着的萘及焦油尘。顶部为煤气进口,下不为煤气出口。其结构与煤气横管初冷器基本相同。 (2)终冷喷洒液泵2台(一开一备),流量20m3/h,扬程50m,配套电机7.5KW。 (3)洗苯塔1台,Dn3.6m;H=32m,洗苯塔的作用是使循环洗油(贫油)和煤气在塔内充分接触,已达到洗苯效果。洗苯塔是用钢板焊制成的直立圆形轻瓷填料塔。 (4)脱苯塔1台,Dn1.6m,,3层塔板,15层塔板以下为提馏段,15层塔板以上为精馏段。每层塔板上均安装泡罩,泡罩上有许多细缝供蒸汽自下而上通过,塔板上还有溢流管供液体自上而下流动,这样气液两相进行传质传热,使液体中低沸点的馏分部分气化,而蒸汽中高沸点馏分则部分冷凝,经过多层塔板如此反复地部分气化和冷凝,结果在塔板液体中富集了高沸点的洗油(此时称为热贫油),在塔顶蒸汽中便富集了低沸点组分的苯蒸汽,从而使富油中粗苯被蒸脱出来。脱苯塔是不锈钢板焊制成的,处理富油能力为45-55m3/h。 (5)管式加热炉1台,总热负荷2.97兆瓦/h,是有对流段和热辐射段的直立圆筒管式炉,其作用是加热富油和将饱和水蒸气加热成过热蒸汽供富油脱苯做直接加热蒸汽用。 (6)热贫油泵和富油泵3台(2开1备),额定流量50m3/h;扬程H=125m,配电机功率37KW。 (7)粗苯回流泵2台(1开1备),额定流量6.25m3/h,扬程=36m,配套电机功率3KW.其作用是向脱苯塔顶送入粗苯做回流,以控制塔顶温度,出合格的产品。 (8)洗油再生器,再生器的作用是除去洗油中高沸点的聚合物组分,以改善循环洗油是质量,同时还向脱苯塔提供直接加热蒸汽,再生器是用钢板焊制成的直立柱筒体,底部为锥形。循环洗油(富油)再生 原理是由于洗油循环加热使用,洗油中高沸点组分聚合作用生成残渣,通过洗油再生器,利用蒸汽热量和蒸吹,将富油中低沸点组分蒸出,且将循环洗油残渣排出。 10.影响洗油吸收粗苯的主要因素 煤气中的粗苯在洗苯塔内被吸收的程度称为回收率。回收率是评价洗苯操作好坏的主要指标,此值可用下式表示: N=1-a2/a1 式中:n——粗苯回收率,% a1、a2——洗苯塔进口煤气和出口煤气中苯含量,g/m3 粗苯回收率的大小取决于下列因素;煤气和循环洗油(贫油)中粗苯含量;煤气流速及压力;循环洗油(贫油)量及其分子量;吸收温度;洗苯塔的构造及填料特性。 一般粗苯回收率为93-95%,适宜的吸收温度为25℃左右,在操作中必须严格控制贫油温度略高于煤气温度,以防止煤气中的水蒸气冷凝而进入循环洗油(富油)中,恶化脱苯系统的操作。一般确定循环洗油量宜按1完m3煤气为15-18t左右,此值称为油气比。贫油含苯量是决定洗苯塔后煤气含苯量的主要因素之一,经理论计算结果表明,若使洗苯塔后煤气含苯量不大于2g/m3,则贫油中的最大粗苯含量0.22%(理论值,实际贫油含苯量可允许达到0.3%—0.5%,仍能保证塔后煤气含量在2g/m3)。 11.洗油的性能要求及质量指标 11.1洗油的性能 为满足从煤气中回收和制取粗苯的要求,洗油应具有如下性能: (1)常温下对粗苯具有良好的吸收能力,在加热时又能使粗苯很好的范例出来; (2)具有足够的化学稳定性,即长期使用中,其吸收能力不降低; (3)在吸收操作温度下,且易与水分离; (4)不与水生成乳化物,且易与水分离; (5)有较好的流动性,以使洗油易于用泵抽送和在洗苯塔内填料上均匀分布。 11.2洗油的质量指标 国内大多数焦化厂用于洗苯的时及哦啊有洗油,也有极少数焦化厂用石油洗油。 焦油洗油是高温煤焦油中230—300℃的馏分,其质量指标如下表所示。 指标名称 指标 指标名称 指标 密度(20℃),g/ml 1.04-1.07 含萘量%(W) ≤13 馏程(%) 粘度E25 2 230℃前馏出量(V) ≤3 水分%(W) ≤1 300℃前馏出量(V) ≥90 15℃结晶物 无 含酚量%(W) ≤0.5 要求洗油的萘含量小于7%,苊含量不大于5%,以保证在10-15℃时无固体沉淀物。萘因熔点较高,在常温下易析出固体结晶,因此,应控制其含量。 但萘与苊、芴、氧芴及洗油中其他高沸点组分混合时,能生成熔点低于有关组分的共熔点混合物。因此,在洗油中存在一定数量的萘,有助于降低从洗油析出沉淀物的温度。洗油中甲基萘含量最高,洗油粘度小,平均相对分子质量小,吸收能力较大。所以,在采用洗油脱萘工艺时(本公司未使用),应防止甲基萘成分随之被切出。洗油含酚高易于水形成乳化物,破坏洗苯操作。另外,酚的存在还易使洗油变稠。因此,应严格控制洗油中含酚量。 12.粗苯生产中常出现的故障及其处理方法 (1)循环洗油含水量过高 会造成脱苯系统操作混乱。处理方法如下: a.及时调整贫油温度高于煤气温度2—5℃; b.清扫终冷塔后煤气管道水封的排液管,使其畅通,防止冷凝水进入洗苯塔底富油中; c.视情况适当提高管式炉后富油温度和脱苯塔顶温度,使循环洗油中水分尽快脱出。 (2)洗苯塔阻力过大 在生产操作中,一般洗苯塔的阻力在500Pa左右,如果过高将影响洗苯效果。降低洗苯塔阻力的方法之一可用热贫油冲洗的办法来降低洗苯塔的阻力。 (3)塔底油槽抽空或冒槽 a.各油泵送油量不一致,导致各油槽液位不稳定,甚至抽空或冒槽,这时应立即调节有关油泵流量,及时倒油。预防方法:平时应稳定各油泵操作,使各油泵的流量保持一致,经常检查液位是否正常。 b.若因液位计不准,应及时检查现场液位计,然后立即倒油。预防方法是经常对照液位计的读数与仪表指示值。 13.洗苯工序对焦炉煤气质量的要求 焦炉煤气中:含氨<0.03—0.1g/Nm3; 萘<0.2—0.5g/Nm3; 焦油<0.05 g/Nm3; 硫化氢<0.2—0.5g/Nm3; 14.洗涤工标准化作业规程 1. 工艺参数 洗苯塔阻力<1000Pa 出终冷塔煤气温度25—28℃ 入洗苯塔贫油温度 27—30℃ 出洗苯塔煤气温度28℃ 洗苯塔操作温度波动范围控制在20—30℃ 洗苯塔前煤气含苯 25—40 g/Nm3; 洗苯塔后煤气含苯≯4 g/Nm3; 贫油中含苯≯0.5% 富油中含苯 1.8—2.5% 富油中含水 ≤1% 循环洗油量50m3/h 泵的电机升温 ≯45℃ 轴承温度≯65℃ 2.正常操作 2.1做一次塔前塔后煤气含苯化验,根据化验结果,结合生产操作情况做适当调整,使塔后煤气含苯符合要求。 2.2做循环洗油分析,掌握循环油量状况及洗苯效果,均匀补充新洗油、加新洗油时防止满油。 2.3观察富油槽液面是否波动并及时调节,杜绝满油。 2.4观察入洗苯塔煤气温度、严格控制入塔煤气温度符合规定。 2.5煤气温度,保证并调整合适的洗油循环量及贫油温、保证塔后煤气含苯符合技术要求、注意洗苯塔阻力情况、若阻力高及时清扫、保证煤气畅通。 2.6每小时巡查各部一次、认真、准确做好记录、每班计量洗油消耗、并做好各项记录。 3.特殊操作 3.1开工:开工前油封、水封注满液体、检查各管道阀门处于开工状态。抽出各煤气出入口及洗油管道盲板那,打开塔顶及煤气出口阀门前放散管阀门,由塔底及管道通入蒸汽,当放散管冒大量蒸汽时稍开煤气入口阀,然后关蒸汽阀。当放散管冒煤气时,做爆炸试验,合格后关闭放散,全开煤气出口阀门,通知鼓风机工注意机后压力变化。然后慢开,煤气入口阀门,同时关闭交通阀。待煤气正常通过后,按以上步骤将洗苯塔送油,当富油槽油面足够时向蒸馏送油。当贫油槽油面达到指标时,打开循环油槽底阀门,关闭新洗油槽底阀门,使循环油槽底的洗油循环使用,并调整各油槽的液面而稳定在规定指标。 3.2停工:停止向塔内喷淋洗油,通知鼓风机工注意机后压力变化,打开煤气交通阀。临时停工时,关闭塔煤气出入口阀门,并留3-6扣保证洗苯塔正压。停塔检修时,则将煤气出入口阀门全关死,打开塔各处放散阀门,通蒸汽赶净塔内煤气,并把出入口煤气阀盲死,在塔内用蒸汽清扫时,塔温未降下来前,严禁卸开踏上任何法兰和关闭踏上任何放散,防止塔内自燃和把塔体抽扁,进塔检修前做空气分析,合格后方可进塔检修。 3.3洗苯塔的清扫(热贫油的清扫):塔阻力增大时,首先停一、二段贫油冷却器冷却水,然后用清扫专业泵进行热油进塔,油从塔顶部雾层之上向下喷油进行循环,直到清扫阻力正常。若2-3小时不成效可停煤气进塔、停蒸馏系统蒸汽,用管式炉将洗油加热到180-220℃循环清扫至阻力正常。(注:用蒸汽清扫仅在检修时使用)。 15.蒸馏工标准化作业规程 1.工艺参数 油气换热器后富油温度 60—70℃ 贫富油换热器后富油温度 120—140℃ 脱苯塔顶部温度 90—93℃ 一段贫油冷却器后贫油温度 38—45℃ 二段贫油冷却器后贫油温度 27—30℃ 脱苯塔底部压力 0.03MPa 再生器顶部压力 0.05MPa 再生器顶部温度 160—190℃ 再生器底部温度 170—200℃ 粗苯冷凝冷却器后粗苯漱口温度 25—30℃ 入再生器富油量 1—1.5m³/h 残渣槽温度 60—80℃ 粗苯回流量 3—5m³/h 2.正常操作 2.1及时调节脱苯塔顶温度,保证符合技术指标。 2.2经常保持整齐压力的稳定,保证个塔温度及压力的温度。 2.3经常检查油气换热器、贫富油换热器,使进出口油温符合规定,发现异常及时处理。 2.4经常检查各油水分离器分离情况,做到油中不带水、水中不带油。 2.5根据季节温度变化,用低温水给苯贮槽降温,及时汇报贮槽液位情况,做好外送与计量。 2.6定时取油样、掌握脱苯效果。 2.7及时做好各种记录(每小时巡查一次)。 2.特殊操作 3.1蒸馏系统开工:开工前对设备管道、阀门及仪表进行仔细检查,并验证可靠。关闭各设备放空管,打开各设备出入口阀及放散管家,将各水封油水分离器注满水。从富油泵出口阀门外侧通蒸汽经油气换热器、贫富油换热器、管式炉到再生器、当再生器放散管冒大量蒸汽时、关闭蒸汽和放散管。从再生器通蒸汽经脱苯塔、贫富油交换器、一段贫油冷却器到贫油槽,当贫油槽放散冒蒸汽时关闭蒸汽。开富油泵使富油通过油气换热器,贫油换热器、管式炉进入脱苯塔、当贫油槽有足够油时开贫油泵,按生产系统流程进行冷油循环、在冷油循环过程中、检查管路流向的法兰、阀门、仪表是否安装严密、设备回油是否正常。待冷油循环30min左右,确认不正常后按管式炉开工顺序进行点火加热、炉内温升速度为3—5℃/min。当管式炉富油温度升到110—120℃时稳定下来操作一段时间。观察其含水大小、放散管是否冒大量蒸汽各部分是否严密、待一切正常后贫油冷却器给冷却水。再将管式炉富油出口温度提到180—185℃。 3.2蒸馏系统停工:停工前放空管保持畅通,再生器停止进油、降低炉膛温度。炉膛温度降至200℃左右时,停止给水。停工时间长,放净系统内所有设备及管道的存油,并通蒸汽清扫,逐渐减少贫油冷凝水量,维持油温合乎洗苯要求,直到贫油冷却器停水。将洗油该洗苯塔内部循环,检查设备时必须堵盲板,通蒸汽清扫,确认无可燃气体,在通风良好的情况下进行。 16.管式炉工标准化作业规程 1.工艺参数 管式炉膛温度 ≯500℃ 管式炉废气温度 300—400℃ 过热蒸汽温度 300—400℃ 管式炉用煤气压力 ≥2.5KPn 管式炉烟囱吸力 -100pa 富油出管式炉温度 180—185℃ 入管式炉煤气压力 4KPa 入管式炉蒸汽压力 0.4—0.6Mpa 入管式炉低压蒸汽量 1-2t/h 2.正常操作 2.1 每小时检查炉膛一次,观察炉管是否局部发红,火焰是否烧偏。 2.2及时清理喷嘴外焦油和地下焦油。 2.3调节煤气总阀、使煤气压力在规定范围内、注意低压报警、注意水封液位。 2.4注意富油出口温度变化,炉膛温度变化、保证富油温度温度在规定指标。 2.5发现事故隐患及时处理。 2.6注意检查再生器液面是否正常,各部位压力是否符合规定,根据油的粘度:呈稀焦油状时,停止加油(每2-3天排渣一次)浓缩后排渣,并及时外送。排净后再打开阀门加油、排渣时直接注意对直接流量的调节。 2.7每小时巡查一次,认真准确做好记录。 3.特殊操作 3.1 管式炉开工:开工前必须检查煤气系统、油系统、蒸汽系统各阀门及烟囱翻板是否具备开工条件。压力计、温度计及自调仪表是否好使,炉膛通蒸汽清扫、当烟囱大量冒蒸汽时关闭蒸汽,给火种、开点火用煤气胶管、侧身将胶管煤气火源移进风口试火,确认煤气阀门不漏 。炉内无残余煤气后,将火源伸入炉膛喷嘴。根据3-5℃/min的加热速度逐渐加大煤气量,视循环油含水情况,在油出口温度达110-120℃恒温脱水。然后再继续升温至富油出口温度符合技术规定。 3.2管式炉停工:关闭煤气喷嘴进口阀门,停止煤气加热关闭煤气总阀,启动调节阀和支管阀门以及调节仪表、富油走旁道,必要时煤气堵盲板。慢开烟道翻板,风门降低炉膛温度、降温速度3-5℃/min冷却时间大于4小时,停工三天课不放油、超过三天应把油放回油槽用蒸汽清扫油管。 3.3管式炉油管漏油着火停炉操作:应立即关闭煤气总阀和煤气之动阀门,打开炉底和对流段油管箱内的消火蒸汽阀门(大于100mm的煤气管要缓慢关闭)情况特别危险时,可打开炉膛下部消火蒸汽,温度降至50℃以下时,全开翻板,打开入孔后方可入内。 3.4管式炉突然停电操作:停电时应立即关闭煤气系统所有阀门,打开地风门和烟道翻板并通蒸汽降低炉膛温度,当炉温降到200℃是关蒸汽,短时间停电做好开炉准备,以待来电开炉,若停电时间长,经领导同意按长时间通过处理。 3.5管式炉突然停火操作:发现有自动熄火时应立即关闭炉前煤气系统各种控制阀、并通知蒸馏工做好调节。打开翻板排净煤气,查找原因并进行处理、处理后按开工规程开炉。 3.6富油泵突然停泵操作:立即关闭煤气各控制阀门、打开翻板和炉膛蒸汽消火阀门进行迅速降温,防止炉内存油结焦。当富油泵排除故障正常运行后打开程序恢复正常。 3.7管式炉停蒸汽操作:属暂时停气,只将再生器直接蒸汽关闭。停气再生器加油和排渣,关死脱苯塔直接蒸汽进出阀门逐渐减少回流量,关小各冷却水量维持生产等待来气,属长时间(4h以上)停气,按停工处理。 3.8管式炉停电操作:立即关闭管式炉加热煤气管阀门,关再生器直接蒸汽,切断电源,关闭进出口阀门,停止再生器加油和排渣。若停电时间长按停工处理。 17.洗涤工岗位职责 1.在工段及本班班长领导下积极参与质量管理、控制、安全生产,完成各项本职工作。 2..负责终冷塔和低温水的调节及冷凝液循环泵的操作,始终冷塔出口煤气温度的稳定。 3.负责洗苯塔、贫油冷却器等操作,使出洗苯塔煤气含量符合技术规定。 4.负责洗苯塔底富油的稳定输送。 5.负责新洗油的接受及定期添加。 6.负责富油、循环洗油、新洗油的化验取样。 7.负责终冷塔上下段、富油槽液位控制积水封槽、油封槽的液位稳定和定期清扫。 8.精心控制、调节各参数,使系统处于最佳生产状态。 9.负责本岗位的正常操作,开停工及特殊操作。 10.负责本岗位生产工具、消防器材的保管,所属设备的维修、点检、如实、准确的做好原始记录,发现问题及时处理、汇报。 18.蒸馏工岗位职责 1.在班长的领导下,完成各项工作。 2.负责富油加热、蒸馏、保证贫油低含苯量。 3.负责向终冷洗苯系统抽送贫油。 4.负责苯蒸汽的冷凝冷却、苯水分离、产品的计量、输送。 5.负责洗油的再生及残渣的排放、输送。 6.负责地下放空槽的液位控制。 7.精心调节各项参数,使系统处于最佳生产状态。 8.负责粗苯、贫油、残渣的化验取样。 9.负责本岗位的正常操作,开停工操作及特殊操作。 10.负责本岗位的环境卫生工作。 19.管式炉岗位职责 1.在班长的领导下完成各项工作。 2.负责脱苯塔、管式炉、油气换热器、产品贮槽、再生器、各油水分离器的操作,保证产品质量合格。 3.负责本岗位的开停、倒换、清扫、维修及事故处理工作。 4.负责本岗位粗苯回收机输送工作,准确计量,并认真填写记录结果。 5.精心填写各参数,使设备处于最佳生产状态。 6.负责本岗位生产工具、灭火器材的保管、维护和使用工具。 7.负责本岗位的环境卫生工作。 20.粗苯工段岗位安全操作规程 1.本岗位属甲类防火区,A级危险区域,禁止烟火,与市场无关人禁止入内。 2.禁止用苯洗手、擦地、清洗设备,禁止用压缩空气吹扫苯管道。 3.严禁用铁质、塑料盒其它能生产火花或静电的工具进行检修、取样和测量。 4.禁止穿钉子鞋、化纤衣服。 5.禁止乱扔工具盒铁质物件。 6.设备的开、停必须按安全规程进行操作。 7.管式炉点火前应用蒸汽将残余煤气吹扫干净,应先送火后开煤气阀。 8.严禁在管式炉烟囱翻板关闭的情况下点火,炉膛不准正压操作。 9.严禁将苯、洗油等易燃、易爆品冲入地沟。 1 改良蒽醌二磺酸钠(改良ADA)法 (1)ADA法脱硫 ADA法脱硫工艺由脱硫再生和废液处理两部分组成 “脱硫部分是以碳酸钠为碱源、ADA为催化剂的氧化法脱 硫脱氰”。多数焦化厂、煤气厂的ADA脱硫装置均配置在 洗苯后,废液处理采用蒸发、结晶法制取Na2S2O3及NaSCN 产品。 脱硫液是在稀碳酸钠溶液中添加等比例的2,6蒽醌 二磺酸和2,7蒽醌二磺酸(A.D.A)的钠盐溶液配置而成。 幻灯片16 改良A.D.A法脱硫工艺 (2)改良A.D.A法 改良A.D.A法是在A.D.A法的基础上发展而来的,与 A.D.A法的主要区别是脱硫液不同。改良A.D.A法的脱硫液在 A.D.A法脱硫液中添加了适量酒石酸钾钠和0.12~0.28%的偏 钒酸钠。 脱硫分三步进行: (a)硫化氢被碳酸钠碱液吸收生成硫氢化钠(NaHS); (b)偏钒酸钠与硫氢化钠反应,生成焦钒酸钠并析出元素硫; (c)焦钒酸钠在碱性脱硫液中被A.D.A法氧化再生成为偏钒 酸钠,得以循环进行。 (3)改良ADA法脱硫工艺的优点: ——脱硫脱氰效率高,可达98%以上,溶液无毒性,处理煤气中硫化氢浓度的适应性以及温度和压力的范围均较广,对设备的腐蚀较轻,副产品硫磺质量较好,双塔串联后煤气中H2S和HCN含量可分别降至20mg/m3和50mg/m3以下,符合城市煤气标准。 ——工艺流程简单,占地少,投资低,可靠性强。 ——产品硫磺质量稳定,品质高。 (4)改良ADA法脱硫工艺的缺点: ——以钠为碱源,碱消耗量大。 ——ADA脱硫装置位于洗苯后即煤气净化流程末端,不能缓解煤气净化系统的设备和管道的腐蚀。 ——废液难处理,必须设提盐装置,增加了投资。 2 HPF法脱硫工艺 HPF脱硫是我国技术人员自行研制开发的采用HPF新型高效复合催化剂从焦炉煤气中脱除H2S和HCN的新工艺。 该工艺是以煤气中的氨为碱源,在HPF的催化作用下分解煤气中的H2S和HCN。 HPF催化剂的主要成分为对苯二酚、PDS、FeSO4。其中,PDS起主要的催化氧化作用;对苯二酚的配入有助于提高脱硫液的流动性,预防堵塞;FeSO4主要用于消泡。煤气中的CO2与NH3在水溶液中生成NH4HCO3和(NH4)2CO3,向溶液中提供了较为稳定的碱源。 HPF法脱硫工艺的优点: 1)脱硫脱氰效率高,塔后煤气中H2S和HCN含量可分别降至200mg/m3和300mg/m3以下。 2)与ADA相比,循环脱硫液中盐类增长缓慢,因而废液量相对较少。 3) 以煤气中氨为碱源,资源利用合理,原材料、动力消耗低。 HPF法脱硫工艺的缺点: 1)塔后煤气H2S含量达不到标准要求,影响用户需要。 2)硫磺品质低、脱硫废液难处理。 3)相对于ADA法,投资大,工艺复杂,对工艺操作要求高,运行稳定性相对较低。 3 AS法脱硫工艺 十多年来,AS法煤气脱硫工艺在我国积累了丰富的操作经验,各项操作指标已达到和接近设计要求。多数厂家塔后煤气含NH3能达到50~30mg/m3, H2S在500mg/m3左右,焦油≤ 50mg/m3,萘≤200mg/m3 。 原石家庄焦化厂1998年10月份的操作数据为:塔后煤气含H2S 250 ~500mg/m3, NH3 40mg/m3左右。 宣钢焦化厂的最好操作指标是塔后含NH3为10~ 20mg/m3,H2S 470mg/m3。 AS脱硫工艺的优点: AS法煤气脱硫工艺从煤气中回收的硫化氢和氨可以根据需要进行多种组合,采用氨分解和硫回收生产元素硫的组合具有流程短、设备少、投资省和占地少等优点,是一种较为经济的组合流程。 AS脱硫工艺的缺点主要存在着堵塞、腐蚀和脱硫效率低等问题。 德国蒂森克虏勃恩库克公司为首钢建设的AS法焦炉煤气净化装置于2003年9月投产。装置采用TKEC公司的CYCLASULFR法脱除煤气中的硫和氨,COMBISLAUSR法分解 NH3 和HCN生产元素硫。该工艺流程有较大改进,而且提高了煤气净化效率和节省了能源。 AS法脱硫工艺流程 4 FRC法脱硫工艺 FRC(苦味酸)法焦炉煤气脱硫脱氰工艺是由弗玛克斯(FUMAKS) 脱硫、洛达科斯(RHODACS)脱氰和昆帕科斯(COMPACS)制取硫酸三法工序组成的一种湿式氧化脱硫脱氰并回收硫磺的高效脱硫脱氰工艺,其工艺流程见图所示。 脱硫脱氰工艺是以苦味酸为催化剂,以煤气中的氨为碱源。 吸收焦炉煤气中的 H2S和HCN。 图 FRC焦炉煤气脱硫脱氰工艺流程图
在线留言订购

资讯中心
- yh86银河国际:深圳 库存回收 2024-03-11
- yh86银河国际:进口轴承回收 2024-03-11
- yh86银河国际:您使用的浏览器可能存在安全风险 2024-03-11
- yh86银河国际:门头沟50平方电缆回收价格轴承黄铜回收 2024-03-11
- yh86银河国际:邢台市临西中国轴承大世界 2024-03-10
- yh86银河国际:轴承钢制品价格 2024-03-10
- yh86银河国际:辽宁轴承回收库存积承回收使用微信扫描二维码分享朋友圈,成交更快更简单! 2024-03-10
- yh86银河国际:风电中最贵的部件 2024-03-10
- yh86银河国际:河北省冀南轴承回收有限公司 2024-03-10
- yh86银河国际:橡胶磨粉机,橡胶粉碎机,轮胎粉碎机,橡胶破碎机,轮胎破碎机,废旧轮胎磨粉机,废旧轮 2024-03-08
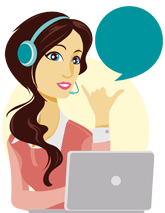